Embarking on a project involving insulated coolroom panels demands a clear understanding of how to join coolroom panels effectively to guarantee airtight, durable, and thermally efficient results. From selecting the right panel thickness and materials to mastering cutting techniques and sealing methods, every step plays a vital role in building a robust coolroom that stands the test of time.
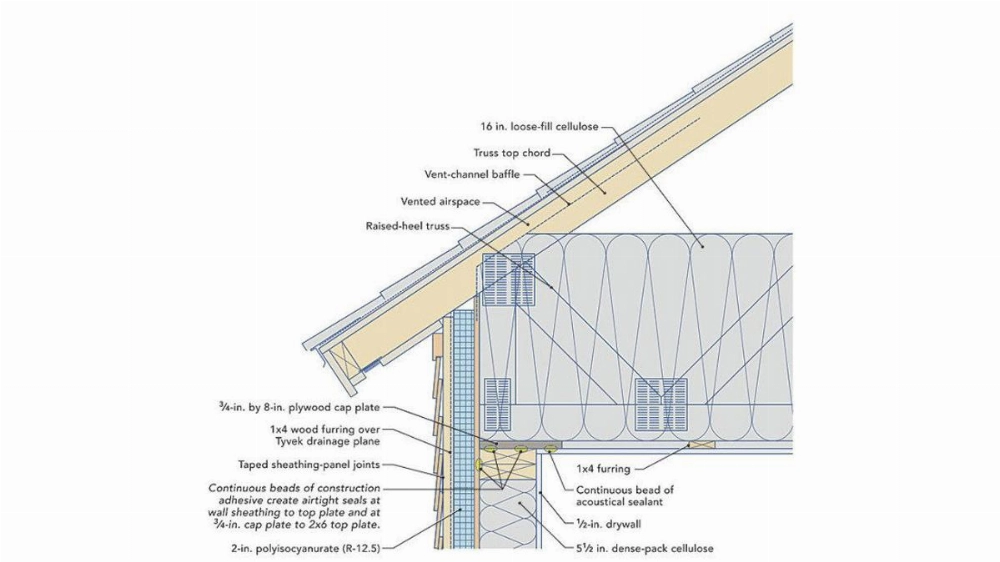
Comprehensive Guide
In this comprehensive guide, I share my experience with various panel brands like Askin and Austec, highlight essential tools and preparation tips, and detail common mistakes to avoid. Whether you’re building a shed from coolroom panels or outfitting commercial refrigeration, mastering how to join coolroom panels correctly is the foundation for success, ensuring optimal insulation and structural integrity.
Selecting the Right Coolroom Panels for Your Project
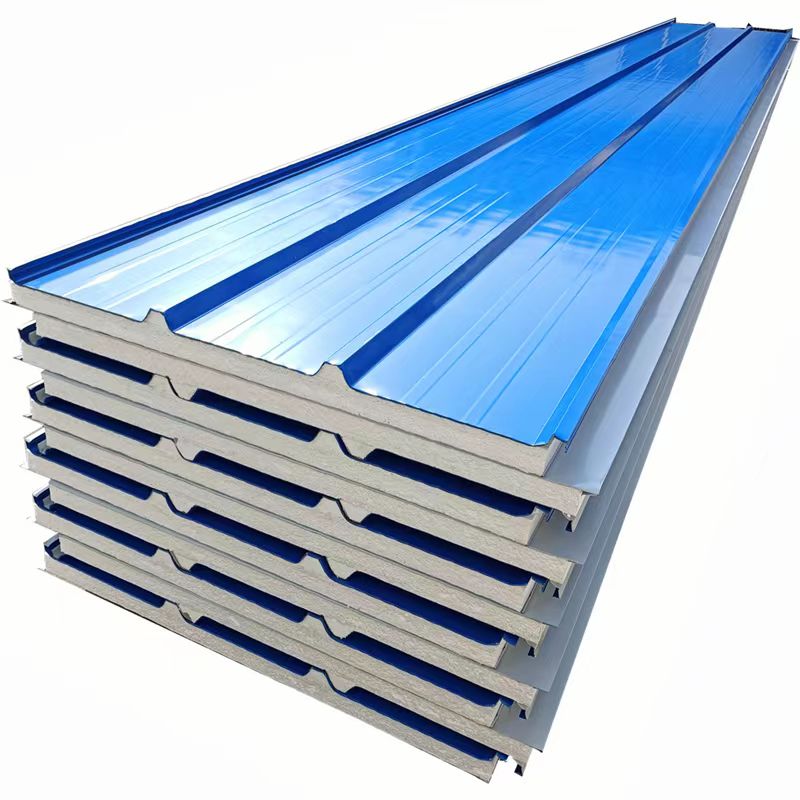
- Parts77 products
- Roof Panel33 products
- Wall Panel99 products
Choosing the appropriate insulated coolroom panels is critical to the overall performance and durability of your installation. Whether you’re building a shed from coolroom panels or fitting out a commercial refrigeration unit, panel selection dictates not only thermal efficiency but also structural integrity and ease of assembly. Having worked extensively with a variety of brands and thicknesses, I’ll guide you through the key factors to consider, referencing standards and popular options such as Askin coolroom panels, Austec coolroom panels, and Austral coolroom panels, which are staples in the coolroom panels NZ and Australian markets.
Understanding Panel Thickness and Insulation Value
Panel Thickness | Common Applications | Thermal Performance | Weight Characteristics (approx.) |
---|---|---|---|
25mm coolroom panels | Cold display cabinets, small freezers | Lower R-value, suitable for less demanding environments | Lightweight, e.g. 25mm coolroom panels Bunnings stock standard |
35mm coolroom panels | Medium-duty coolrooms, flexible use cases | Moderate insulation effectiveness | Moderate weight, easier to handle onsite |
50mm coolroom panels | Standard commercial coolrooms, high insulation needs | High thermal resistance | Typical 50mm coolroom panel weight ranges from 8 to 12 kg/m² |
75mm coolroom panels | Cold storage requiring enhanced insulation, freezer rooms | Superior R-values for energy savings | Heaviest; requires careful handling |
100mm coolroom panels | Highly specialized or large-scale cold storage | Maximum insulation capacity | Considerably heavy, needs strong framing support |
Selecting the correct panel thickness is paramount. For example, in Perth, 50mm coolroom panels are widely used due to their balance of performance and manageability. The differences in panel thickness often influence the structural design and also the best way to cut coolroom panels, which varies depending on density and composite materials.
Material and Facing Options
Most aluminium coolroom panels are favored for their corrosion resistance and lightweight durability. Brands such as Askin and Austec offer aluminium-faced panels that provide an excellent surface for painting coolroom panels if desired, which is beneficial for bespoke aesthetic or branding needs.
Within the industry, panels may have facings from either aluminium or steel, each with specific advantages:
Facing Material | Benefits | Typical Use Cases |
---|---|---|
Aluminium | Corrosion resistant, lightweight, suitable for wet environments | Food industry coolrooms, pharmaceutical storage |
Steel (galvanized or painted) | High strength, cost-effective, can be finished for aesthetics | Warehouse cold storage, industrial freezers |
Brand Selection and Availability Considerations
When sourcing your panels, consider availability and support in your region. For example:
- Coolroom panels Sydney suppliers often stock a wide range of 50mm coolroom panels for sale given the high commercial demand.
- Coolroom panels NZ markets feature trusted Austral and Austec products, valued for local compliance and performance standards.
- Specialty or custom dimension panels (such as 25mm or 75mm coolroom panels) might require direct ordering from manufacturers like Australian Coolroom Panels Pty Ltd.
Additionally, analyze your project’s specific requirements in terms of size, temperature control, and ease of installation. This will dictate whether standard panels meet needs or if custom sizing and cutting—knowing how to cut coolroom panels effectively—is necessary on site.
Essential Tools and Materials Needed for Joining Coolroom Panels
Choosing the Appropriate Panels and Cutting Tools
Before commencing any installation, it is vital to select the correct type and thickness of insulated coolroom panels to suit the specific project demands. Common thicknesses include 25mm coolroom panels often found at suppliers like 25mm coolroom panels Bunnings, 35mm coolroom panels, 50mm coolroom panels, and heavier-duty options such as 75mm coolroom panels. The panel choice should align with the insulation requirements and structural stability needed.
When it comes to how to cut coolroom panels, precision tools are essential. The best way to cut coolroom panels usually involves a high-quality circular saw fitted with a fine-toothed blade or a specialized panel saw that minimizes chip-out and maintains edge integrity. For aluminium coolroom panels, a blade suited for metal cutting is necessary to avoid damaging the panel surface.
Hand and Power Tools for Secure Joining
Effective joining requires an assortment of hand and power tools. Standard items include a tape measure, spirit level, square, and chalk line for accurate alignment. An electric drill with appropriate drill bits is needed for pilot holes and fixing fasteners without cracking or splitting the panel edges.
Fastener types vary depending on the panel manufacturer and substrate. Commonly, self-tapping screws or clinch fasteners compatible with the panels’ core and skins are used. Always ensure the fasteners are corrosion-resistant as per local climate conditions.
Sealing and Finishing Materials
To maintain insulation efficiency and air tightness where panels join, high-quality sealants and gaskets are necessary. Polyurethane or silicone-based sealants are commonly preferred due to their flexibility and long-term durability. Specialty joint tapes designed for coolroom panels NZ or coolroom panels Sydney climates can also enhance sealing performance.
Additionally, some projects may require the application of paints formulated specifically for coolroom environments. When painting coolroom panels, it is important to use coatings that do not degrade the panel’s thermal properties or cause patch peeling over time.
Panel Handling and Support Equipment
Given the often substantial dimensions and weight of panels—for instance, the 50mm coolroom panel weight can be significant—handling equipment such as suction lifters, panel clamps, and scaffolding supports is essential. These tools ensure safe manipulation of panels during installation to avoid damage and optimize alignment.
Specialist Panel Brands and Variations
Familiarity with market variations helps to source the correct materials and joinery components. Some well-known Australian suppliers and brands such as Askin coolroom panels, Austec coolroom panels, Austral coolroom panels, and Australian Coolroom Panels Pty Ltd offer proprietary fixing systems and accessories designed for their particular panel ranges. Using manufacturer-recommended tools and materials will enhance joint integrity and overall performance.
Preparing Panel Edges for a Secure Fit
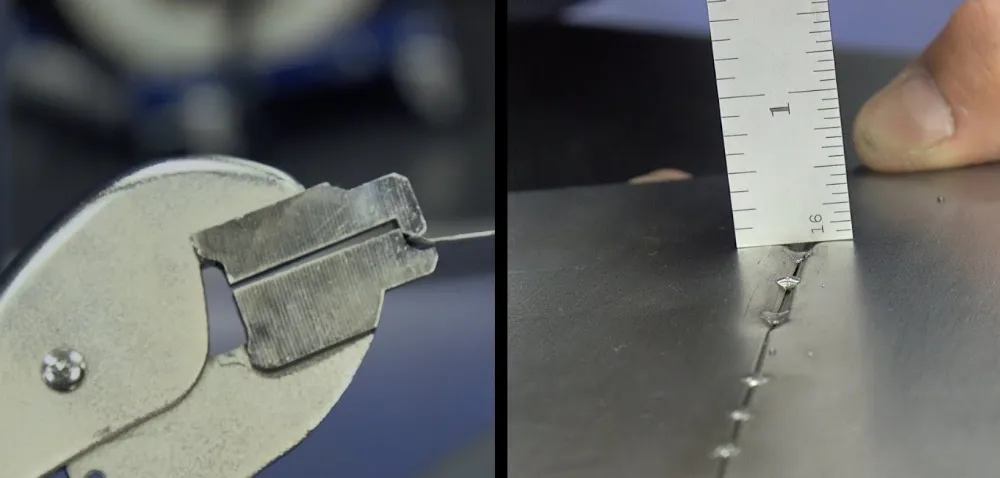
Proper preparation of insulated coolroom panels edges is critical to achieving a tight, durable joint that ensures maximum insulation efficiency and structural stability. Whether working with 50mm coolroom panels, 100mm coolroom panels, or thinner options such as 25mm coolroom panels or 35mm coolroom panels, edge preparation must be precise to accommodate the specific panel thickness and material characteristics.
Edge Inspection and Cleaning
Begin by thoroughly inspecting the panel edges for any damage, dents, or contamination. Foreign particles can compromise the seal and fit. Use a clean, dry cloth to wipe away dust, grease, or residue, especially important when handling aluminium coolroom panels or panels from suppliers like Askin coolroom panels, Austec coolroom panels, or Austral coolroom panels. Clean edges provide a uniform bonding surface for sealants and adhesives, preventing air leaks and moisture ingress.
Cutting and Trimming Edge Accuracy
Achieving a secure fit requires correctly sized and squared panel edges. The best way to cut coolroom panels depends on the core material and facing type. For panels with thicker insulation cores such as 75mm coolroom panels or 50mm coolroom panel perth models, a fine-toothed circular saw or panel saw with an appropriate blade for foam and metal facings is recommended.
Below is a guide to selecting cutting tools based on panel thickness:
Panel Thickness | Recommended Cutting Tool | Notes |
---|---|---|
25mm Coolroom Panels (e.g., 25mm coolroom panels Bunnings) | Fine-toothed handsaw or power saw with metal-cutting blade | Suitable for small adjustments and trimming |
35mm & 50mm Coolroom Panels | Circular saw with foam blade or specialized coolroom panel saw | Reduces edge chipping and provides clean straight cuts |
75mm & 100mm Coolroom Panels | Panel saw with carbide-tipped blade | Essential for cutting thicker cores and maintaining panel integrity |
When cutting, maintain firm control of the panel to avoid excessive vibration or edge splitting. Use straightedge guides to ensure perfectly square edges, as even slight deviations can compromise joint tightness during assembly.
Edge Profiling and Joint Preparation
Many Australian coolroom panels Pty Ltd products come with pre-formed edge profiles such as tongue-and-groove or lap joints. If custom cutting or adjustments are necessary, recreating these profiles accurately is paramount for joining. Utilize template guides or routers where needed to replicate factory-standard profiles.
For panels without factory profiling, mechanically smooth raw edges using fine-grit sanding tools or files to soften sharp corners. This prevents cutting or tearing of joint sealants and eases panel alignment during installation.
Priming and Preparing Surfaces
Prior to joining, treating panel edges with a compatible primer enhances adhesion of sealants and joint tapes. This is especially important with painting coolroom panels as primers promote lasting bond strength. Consult manufacturer datasheets for recommended primers, particularly when working with unique facings such as aluminium or composite materials.
Handling and Storage Considerations
To maintain edge condition, store coolroom panels Sydney and coolroom panels NZ in dry, flat areas off the ground on supports. Avoid stacking heavy loads that may crush or deform panel edges. Proper storage mitigates damage before installation.
Summary Table: Edge Preparation Checklist
Step | Description | Purpose |
---|---|---|
Inspection | Check edges for damage, clean surface | Ensure clean bonding surface |
Cutting | Trim edges with appropriate saw and blade | Maintain straight, square edges |
Edge Profiling | Shape edges to match joint profiles | Enable secure panel interlock |
Sanding/Smoothing | Remove sharp edges and burrs | Protect sealants and ease assembly |
Priming | Apply suitable primer on edges | Promote sealant adhesion |
Storage | Store panels flat, dry, and protected | Prevent damage prior to fitment |
By following these meticulous edge preparation steps, whether assembling a small cold storage unit or building a shed from coolroom panels, one ensures that subsequent joining and sealing steps perform optimally. Proper edge preparation is the foundation for a robust, air-tight coolroom structure.
Step-by-Step Guide to Aligning Coolroom Panels Correctly
Preparing the Installation Area
Before beginning the alignment process, ensure that the installation surface is clean, level, and free of debris. This is crucial when working with insulated coolroom panels such as 100mm coolroom panels or thinner options like 25mm coolroom panels often available at outlets like 25mm coolroom panels Bunnings. Having a stable base prevents misalignment and gaps that could compromise insulation efficiency.
Positioning Panels for Initial Placement
Start by positioning the first panel firmly in place. For projects involving building a shed from coolroom panels or installing aluminium coolroom panels, a precise initial placement sets the tone for subsequent panel alignment. Panels such as 35mm coolroom panels, 50mm coolroom panels, or 75mm coolroom panels should be handled carefully due to their varying weights — for instance, understanding 50mm coolroom panel weight helps ensure safe maneuvering.
Using Alignment Aids and Tools
Employ tools like spirit levels, straight edges, and clamps to maintain correct alignment during panel installation. Clamping panels at joints helps hold them securely as they are fastened together. When working with brands such as Askin coolroom panels, Austec coolroom panels, or Austral coolroom panels, it’s important to refer to specific manufacturer guidelines for alignment tolerances and recommended techniques.
Ensuring Proper Panel Joint Fit
Align each panel’s tongue and groove or tongue and groove lock system precisely. This ensures a tight joint, which is critical for maintaining the coolroom’s thermal performance. Knowledge of how to cut coolroom panels accurately becomes essential when custom fitting panels on-site, especially if modifications are required to fit unique room dimensions. The best way to cut coolroom panels involves using specialized saws designed for insulated panels to avoid damage.
Adjusting Panels for Consistent Seams
Check the seams between panels for uniformity. Misaligned edges can create air leaks or thermal bridges. Using shims or adjusting fixing points allows for precise realignment. Attention to detail is key when working with coolroom panels Sydney suppliers or installing coolroom panels NZ projects, where climate conditions demand high insulation standards.
Final Alignment Verification Before Sealing
Before proceeding to joint sealing and fastening, perform a comprehensive inspection of the panel alignment. Employ a laser level or straight edge to confirm panels are flush both vertically and horizontally. This step minimizes future issues related to panel movement or insulation inefficiency, especially important for australian coolroom panels pty ltd installations that require adherence to strict building codes.
Techniques for Sealing Joints to Ensure Insulation Efficiency
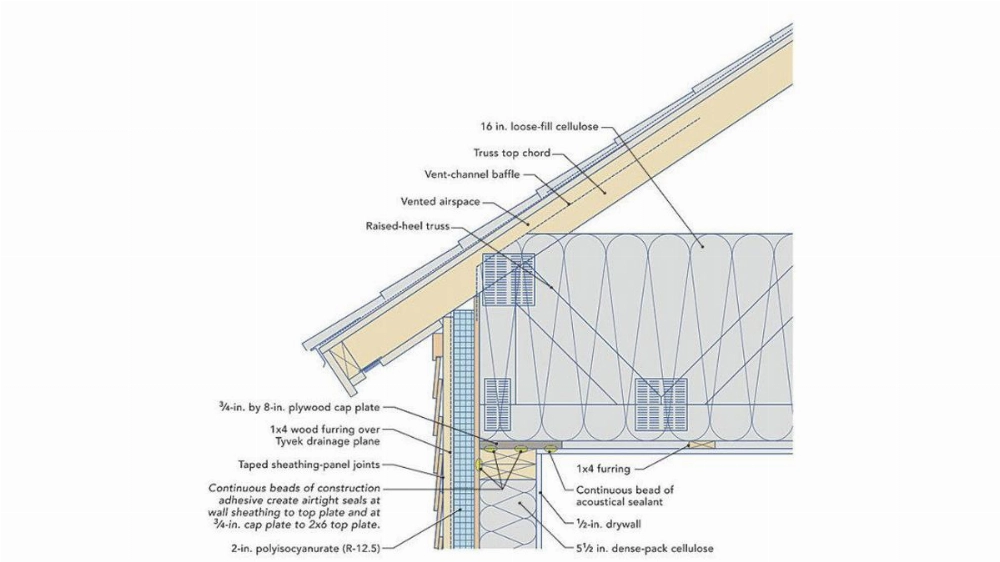
Ensuring the integrity of joints between insulated coolroom panels is critical to maintaining the overall thermal performance and energy efficiency of the coolroom. The correct sealing technique prevents air leakage, condensation, and potential moisture ingress, which can compromise insulation properties. Here, I outline the most effective methods and materials to seal joints, particularly for widely used thicknesses such as 100mm coolroom panels, 50mm coolroom panels, and thinner options like 25mm coolroom panels used in various regions including coolroom panels Sydney and coolroom panels NZ.
Choosing the Appropriate Sealant Materials
The correct sealant depends on panel type and environmental conditions where the coolroom is located. For instance, aluminium coolroom panels and composite panels like Askin coolroom panels or Austec coolroom panels may have different compatibility requirements with sealants. Commonly used sealing materials include:
Sealant Type | Properties | Recommended Usage |
---|---|---|
Polyurethane Foam Sealant | Expandable, excellent adhesion, moisture resistant | Fills gaps for panels such as 50mm coolroom panels for sale and 75mm coolroom panels |
Silicone Sealant | Flexible, UV resistant, durable | Ideal for external joints or where slight movement occurs |
Butyl Tape | Highly adhesive tape, water resistant | Used on flat surfaces, ideal for sealing edges in building a shed from coolroom panels |
Polyisocyanurate (PIR) Joint Tape | Good thermal insulation, rigid | Suitable for joints in insulated coolroom panels requiring additional insulation |
Surface Preparation for Effective Sealing
Before applying any sealant, jointly preparing the panel edges is essential to ensure maximum adhesion and durability. This includes:
- Cleaning: Remove any dust, oils, or contaminants from panel edges using a suitable solvent.
- Drying: Ensure surfaces are completely dry, especially when working with products like 25mm coolroom panels Bunnings which may be stored in humid conditions.
- Sanding or Light Abrading: For aluminium coolroom panels, lightly abrading smooth surfaces can improve sealant grip.
Applying Sealants to Panel Joints
When joining panels such as 35mm coolroom panels or the heavier options like 50mm coolroom panel Perth sizes, the sealant must fully fill the joint gap without voids. Key points include:
- Apply sealants continuously along the mating edges rather than in patches to prevent thermal bridges.
- Use backer rods where joint gaps exceed 10mm to optimize sealant thickness and flexibility.
- For tapes, apply pressure evenly and ensure no air bubbles remain trapped beneath.
Special Considerations for Different Panel Thicknesses
Panel Thickness | Sealing Technique | Notes |
---|---|---|
25mm Coolroom Panels | Use compressible butyl tape and silicone sealant on edges | Commonly found in lighter storage coolrooms; easy to cut and seal |
50mm Coolroom Panels | Polyurethane foam sealant with PIR joint tape overlay | Balance between insulation and ease of handling; watch out for 50mm coolroom panel weight during installation |
75mm – 100mm Coolroom Panels | Combination of foam spray fill and elastomeric sealants | Used for higher insulation requirements, typical in commercial coolrooms |
Protective Measures Post-Sealing
Once sealed, it is advisable to protect the joint from mechanical damage and environmental exposure. Applying a suitable primer or conducting painting coolroom panels after sealing ensures enhanced durability and aesthetic finish. For example, australian coolroom panels pty ltd products often come with recommended paint systems tailored to their panel finishes.
Securing Panels Together: Fasteners and Fixing Methods
When joining insulated coolroom panels, selecting the appropriate fasteners and fixing methods is critical to maintaining the structural integrity and thermal efficiency of the coolroom. The choice largely depends on the panel thickness—whether 25mm coolroom panels, 50mm coolroom panels, or even 100mm coolroom panels—as well as the type of material used, such as aluminium coolroom panels or those manufactured by well-known brands like Austec coolroom panels and Austral coolroom panels.
Fastener Types and Materials
Self-drilling screws are the most commonly used fasteners for coolroom panel assembly. These screws often feature a neoprene or EPDM washer that helps form a watertight seal around the fastener penetration, which is essential for preventing air leaks and maintaining insulation performance. Stainless steel or galvanised screws are preferred to resist corrosion, especially in humid environments typical of coolroom applications.
For 50mm coolroom panel weight considerations, thicker panels require longer screws to penetrate sufficiently into structural framing without compromising the panel core. For example, when working with 50mm coolroom panel perth retailers supply, it’s important to match fastener length to the panel thickness plus the substrate thickness.
Fixing Methods
The most effective fixing method involves fastening panels directly to a stable framing system, such as a steel or aluminium framework. This applies to both wall and ceiling panels. Panels should be fixed at every stud or frame member to avoid movement or gaps forming over time.
When working on projects like building a shed from coolroom panels, ensuring uniform fastener spacing—typically around 300mm to 400mm apart—is essential. This ensures even load distribution and minimizes panel flexing which could compromise the seams.
Panel Edge Considerations and Joint Reinforcement
Thicker panels such as 75mm coolroom panels or 100mm coolroom panels require particular attention to joint alignment before fastening to prevent undue stress on the fasteners. In some cases, additional mechanical fixing such as brackets or clips may be used at corners or ceiling joints for reinforcement.
It’s important to consider the fastener’s impact on finishing processes, especially if painting coolroom panels is planned. Using concealed fasteners or covering exposed heads with compatible sealants or caps can improve the aesthetic and reduce maintenance.
Special Considerations for Various Panel Types
For panels like aluminium coolroom panels or specialty products such as Askin coolroom panels, manufacturer guidelines should always be consulted to confirm suitable fixing types, as some aluminium panels require non-magnetic fasteners or special washers to prevent galvanic corrosion.
When working with 25mm coolroom panels Bunnings stocks, these panels are usually lighter and may demand different fixing protocols compared to heavy-duty insulated panels. Always verify the recommended screw length and type to match panel density and application.
Inspecting and Testing Panel Joints for Air Tightness and Stability
Visual Inspection of Coolroom Panel Joints
Once the insulated coolroom panels are joined, the first step is a thorough visual inspection to identify any visible gaps, misalignments, or areas where the sealant might be insufficient. Special attention should be given to the corners and edges where 25mm coolroom panels Bunnings or other thickness variants like 50mm coolroom panels are connected, as these areas are prone to minor misfits.
Look for the following signs:
Inspection Aspect | What to Check |
---|---|
Gap Size | Ensure no visible gaps exceed 2mm between panels, which could compromise insulation. |
Sealant Coverage | Uniform application along the joint, free of cracks or voids. |
Panel Alignment | Panels such as aluminium coolroom panels and foam-filled ones like asksin coolroom panels should be flush without warping. |
Air Tightness Testing
To ensure the coolroom maintains efficient temperature control, air tightness of the joints is crucial. The best practice includes:
- Smoke Test: Introduce smoke near the joints and observe for any leakage points.
- Infrared Thermography: Use an infrared camera to detect cold spots that indicate air infiltration.
- Blower Door Test: This method pressurizes the room and measures leakage rates around the 75mm coolroom panels or other panel sizes.
These tests are especially important when working with coolroom panels Sydney or installations involving 100mm coolroom panels in climates requiring strict temperature regulation.
Mechanical Stability Checks
Assessing stability involves ensuring that panels are securely fixed and can resist typical loads without movement. Key parameters to verify include:
Parameter | Assessment Method | Recommended Standard |
---|---|---|
Fastener Tightness | Manual torque check on screws and bolts used on 50mm coolroom panel weight bearing points. | Screw manufacturers’ recommended torque values, typically 3-5 Nm. |
Panel Deflection | Apply a controlled lateral load and measure movement; should be less than 2 mm. | Building code requirements for insulated coolroom panels. |
Joint Compression | Check for consistent compression of sealant and foam to avoid gaps over time. | Sealant manufacturer’s guidelines, usually 10-15% compression. |
Documentation and Record-Keeping
For ongoing maintenance and warranty purposes with suppliers like austec coolroom panels or austral coolroom panels, keeping a detailed inspection log is advisable. Include:
- Panel types and thicknesses (e.g., 35mm coolroom panels, 50mm coolroom panel Perth products)
- Test results for air tightness and stability
- Notes on any corrective actions taken
Special Considerations for Panel Variants
Different panel types require adapted inspection techniques:
Panel Type | Inspection Focus |
---|---|
Aluminium Coolroom Panels | Check for proper sealing of metal overlaps and avoid scratches before painting coolroom panels. |
Askin/Austec/Austral Coolroom Panels | Ensure foam core integrity and continuous sealant coverage at joints. |
Varied Thickness Panels (25mm, 35mm, 50mm, 75mm) | Test compression and fit to avoid insulation loss at junctions caused by differing thicknesses. |
Common Mistakes to Avoid When Joining Coolroom Panels
Incorrect Panel Selection and Sizing
One of the primary errors made during the assembly process is choosing the wrong type or size of coolroom panels. For example, mixing 25mm coolroom panels with 100mm coolroom panels without proper consideration can lead to uneven insulation and compromised thermal efficiency. Additionally, purchasing panels not suited to your climate or project requirements—such as sourcing coolroom panels Sydney for a build intended for Perth’s conditions—may reduce the lifespan and effectiveness of the coolroom.
Poor Edge Preparation and Misalignment
Failing to adequately prepare the panel edges before joining is a frequent cause of weak joints. Misalignment during installation can cause gaps that reduce air tightness and insulation performance. Ensuring edges are clean, cut correctly using the best way to cut coolroom panels, and fully aligned before sealing is crucial.
Improper Cutting Techniques
Using incorrect tools or techniques when cutting panels—whether 50mm coolroom panel Perth standards or thinner panels such as 25mm coolroom panels Bunnings—often results in rough or uneven edges. This not only complicates the joining process but may also damage panel facings, such as the foam core or aluminium skins on aluminium coolroom panels. Consistently applying recommended cutting methods prevents this issue.
Insufficient Sealing of Joints
Sealing is essential to maintain the integrity of insulated coolroom panels. Skipping or poorly applying sealants leads to air leaks and reduced insulation continuity. Given the variety of panels, such as 75mm coolroom panels or 35mm coolroom panels, ensuring the use of compatible sealing materials designed for each thickness and type is vital. Askin coolroom panels or austec coolroom panels might have specific recommendations worth following.
Overlooking Fastener Compatibility and Placement
Using incorrect or inadequate fasteners can compromise joint stability. For example, choosing fasteners unsuitable for 100mm coolroom panels or heavier options like 50mm coolroom panels for sale without verifying their holding capacity causes panels to shift or separate. Placement of fixings should avoid weakening the panel cores or facings, especially with Australian Coolroom Panels Pty Ltd specifications.
Neglecting Panel Weight and Structural Considerations
Ignoring the weight differences—such as between 50mm coolroom panel weight variations—can result in structural stress if the supporting frame is inadequate. This mistake might occur when building a shed from coolroom panels without accounting for the cumulative load of insulated coolroom panels. Correctly matching panel thickness and weight to structural support ensures long-term stability.
Failing to Inspect and Test Joints Thoroughly
Not conducting thorough inspection and testing after assembly often leads to unnoticed air tightness issues or weak joints. It is essential to check every joint on Austral coolroom panels or any other brand to confirm they meet insulation and stability standards.
Neglecting Surface Treatment Post-Installation
Once panels are joined, neglecting adequate surface treatment such as painting coolroom panels can accelerate wear and reduce durability, particularly with metal-faced panels like aluminum. Proper finishing extends the life of the coolroom and maintains aesthetic standards.
Common Mistake | Impact | Recommended Action |
---|---|---|
Incorrect panel size/type selection | Poor insulation and fit | Match panel thickness and brand to project specs |
Improper edge preparation | Weak joints and gaps | Clean, correctly cut, and align edges before joining |
Poor cutting technique | Damaged panels and misfits | Use recommended tools and methods for cutting |
Insufficient sealing of joints | Air leaks and insulation loss | Apply correct sealants suitable for panel type/thickness |
Wrong fastener selection | Panel instability | Use fasteners compatible with panel weight and material |
Ignoring panel weight & support | Structural stress and damage | Ensure building framework accommodates panel load |
Lack of inspection/testing | Unnoticed leaks and instability | Inspect all joints thoroughly post-installation |
Neglecting painting/surface treatment | Premature deterioration | Apply protective coatings after joining |
My brother recommended I might like this blog.
He was totally right. This post truly made my
day. You can not imagine simply how much time I had spent
for this info! Thanks!
Thanks for the good writeup. It in fact used to be a leisure account it.
Look complex to far brought agreeable from you! By the way, how can we be in contact?