Cutting coolroom panels might seem straightforward, but mastering how to cut coolroom panels properly ensures clean edges, maintains insulation integrity, and prevents costly mistakes. Drawing from extensive hands-on experience, this article unveils the essential tools, precise measuring techniques, effective cutting methods, and safety tips to help you achieve professional results whether using standard 25mm panels or thicker 50mm coolroom panel bunnings stock.
From selecting the right saw blade to supporting panels securely during cutting, every step is crafted to avoid damage and maximize efficiency. Whether you’re working with eps coolroom panels, bondor coolroom panels, or sourcing coolroom panels perth wa styles, this guide empowers you to handle and cut your panels like a pro—saving time, reducing waste, and delivering flawless coolroom panel installations.
Essential Tools Needed for Cutting Coolroom Panels
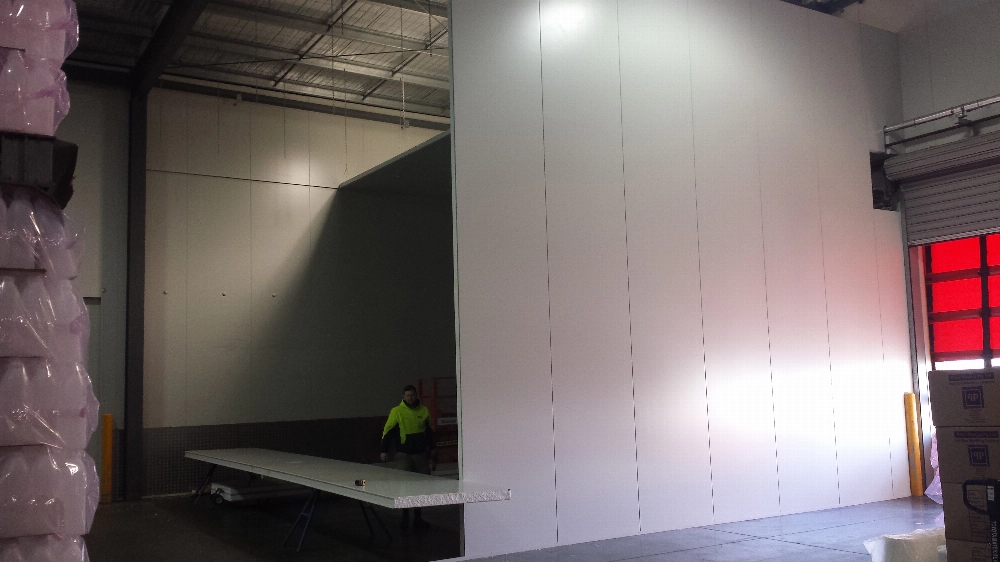
When working on building with coolroom panels, having the right tools is fundamental to achieving precise cuts and maintaining the integrity of the panels, whether you’re dealing with 50mm coolroom panel bunnings stock or sourcing coolroom panels perth styles. Based on my experience, I always ensure that the following tools are available before starting any cutting operation on coolroom panel materials, including eps coolroom panels and bondor coolroom panels.
Cutting Tools
Tool | Use | Recommended For |
---|---|---|
Utility Knife / Heavy-Duty Cutter | Scoring foam core and initial panel surface cuts | 25mm coolroom panels, thin or lightweight panels |
Fine-Toothed Handsaw | Manual cutting for light metal or aluminium faces | Smaller panels or precision cuts on coolroom panels perth wa products |
Power Saw (Circular or Jigsaw) with Metal Cutting Blade | Cutting through metal or aluminium facings efficiently | 50mm coolroom panel for sale types, thick panels, and sandwich panels |
Panel Cutter (Specialised) | Designed specifically for scoring and snapping coolroom panels | Professional use, especially for batches of coolroom panels bunnings |
Measuring and Marking Tools
Accurate measurement is critical to avoid material waste and ensure a proper fit especially when using coolroom panels victoria or sourcing from areas like coolroom panels melbourne and coolroom panels adelaide. The essentials include:
- Measuring Tape: A reliable steel tape measure is indispensable, preferably a 5m or longer length to suit larger panels.
- Square or T-Square: To mark perfectly perpendicular lines for clean cuts.
- Permanent Marker or Grease Pencil: For marking cut lines clearly on metal-faced panels.
Safety Equipment
Handling cutting tools and sharp panel edges comes with inherent risks. For safe operations, I always recommend:
- Safety Glasses: Protect your eyes from dust, metal shavings, and fragments.
- Gloves: Cut-resistant gloves provide essential protection when handling and cutting coolroom panelling.
- Dust Mask: To avoid inhalation of foam or metal dust during cutting, especially indoors.
- Hearing Protection: Required when using power saws for metal cutting.
Support and Handling Tools
Cutting large or thick panels such as 50mm coolroom panel requires steady support to prevent damage:
- Sawhorses or Work Tables: Provide a stable surface and leverage for safer cutting.
- Clamps: Secure panels in place to avoid movement during cutting.
In summary, having the right combination of cutting implements, measuring tools, safety equipment, and supports is vital to successfully cut coolroom panels without damaging their structure or compromising insulation. This ensures professional results whether you’re working with locally sourced coolroom panels perth or considering options like second hand coolroom panels for sale for cost-effectiveness, and properly managing coolroom panels price factors in your project planning.
Measuring and Marking Techniques for Accurate Panel Cuts
Accurate measurement and precise marking are fundamental when working with coolroom panels, whether you are dealing with 50mm coolroom panel bunnings stock or sourcing from specialized suppliers offering coolroom panels perth wa or coolroom panels melbourne. Before initiating any cuts, ensure that the workspace is level and well-lit, as this greatly aids precision.
Choosing the Right Measuring Tools
Using reliable measuring instruments is crucial to avoid costly errors. A high-quality steel tape measure is preferred over fabric tapes for its rigidity and accuracy. For marking straight lines, a long aluminium straight edge or a T-square designed for panel work helps maintain alignment. If dealing with 25mm coolroom panels or eps coolroom panels, which often come in specific thicknesses, double-check measurements against manufacturer specifications.
Establishing Reference Points
Begin by determining all necessary dimensions for the panel installation, bearing in mind the specific thickness of panels like bondor coolroom panels or 50mm coolroom panel for sale models. Mark your initial measurements lightly with a pencil to allow adjustments if needed. When measuring for a coolroom panel shed or other structures, confirm that all adjoining and framing are accounted for. Using chalk lines can assist in marking longer cutting paths, especially for larger panels from suppliers such as coolroom panels adelaide or coolroom panels victoria.
Marking Techniques for Different Panel Types
For standard foam-core coolroom panels, mark the cutting line clearly on the metal or aluminium facing using a fine-tipped marker or pencil. This ensures visibility without damaging the panel surface. When working with second hand coolroom panels for sale, be mindful that existing wear may make lines less visible; enhance marks accordingly. Coolroom panelling often comes with protective films—always through these precisely along your marked lines to maintain integrity.
Verifying Measurements Before Cutting
Adopting “measure twice, cut once” approach is essential. After initial marking, re-measure key dimensions and cross-check angles to guarantee that all lines align with the intended installation design. This step is particularly important when considering coolroom panels price and availability—preventing material waste is a priority. If possible, use a carpenter’s square or digital angle finder to confirm angles for compound cuts.
Summary
- Utilize precise, rigid measuring tools suitable for panel thickness (e.g., measuring 50mm coolroom panel thickness).
- Lightly mark all measurements first, then finalize with a visible yet non-damaging marker.
- Account for panel protective layers and surface finish when marking.
- Double-check measurements and angles, especially when integrating panels from various suppliers such as coolroom panels perth or sourcing coolroom panels for sale.
- Maintain a clean, well-organized workspace marking to reduce errors during cutting.
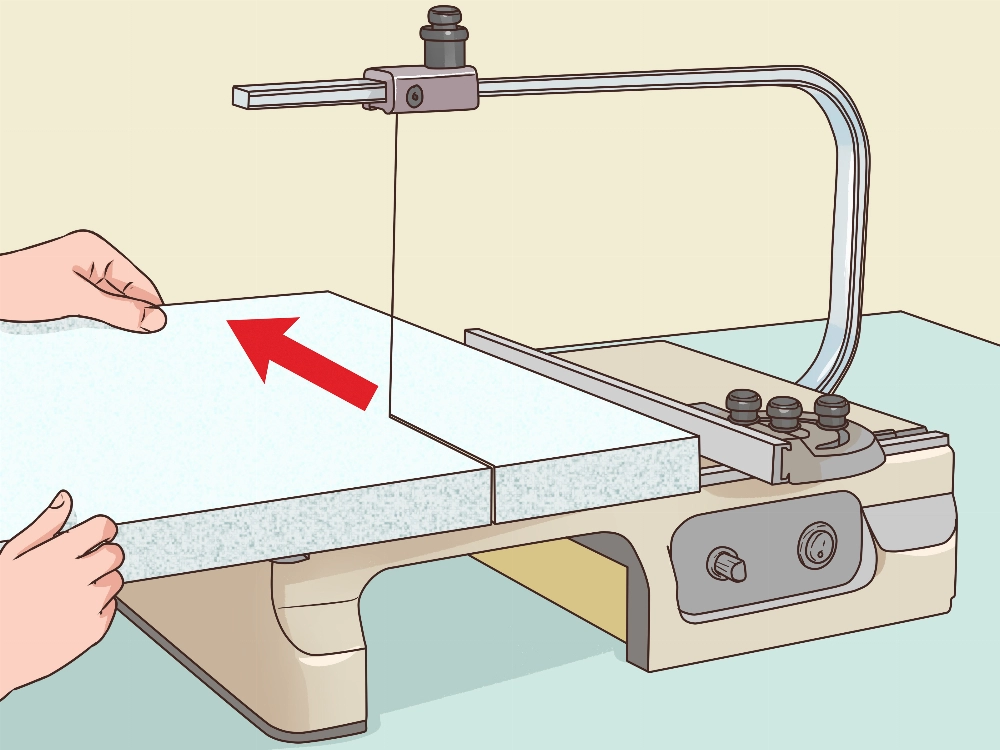
When it comes to cutting coolroom panels, particularly those with a foam core such as EPS coolroom panels or Bondor coolroom panels, precise scoring and cutting is essential to ensure clean edges and maintain the insulation integrity. Whether working with 25mm coolroom panels or the more common 50mm coolroom panel thicknesses found at suppliers like coolroom panels Bunnings or specialized outlets in areas such as coolroom panels Perth and coolroom panels Melbourne, the following method provides a reliable approach.
Tools Required
Tool | Purpose |
---|---|
Utility Knife with Replaceable Blades | Scoring and initial cutting of foam core |
T-Square or Straight Edge | Ensures straight and accurate marking |
Measuring Tape | Accurate measurement of panel dimensions |
Clamps or Weights | Secure panels during scoring |
Work Gloves | Protect hands during cutting |
Step 1: Preparing the Panel and Workspace
Begin by laying the coolroom panel flat on a stable work surface. For best results—especially when dealing with larger sheets such as 50mm coolroom panel for sale commonly stocked in coolroom panels Adelaide and Victoria—ensure the panel is well supported over its entire area to prevent bending or damage. Clear the surface of any debris that could alter your score line.
Step 2: Measuring and Marking
Measure the desired cut length or width accurately using a measuring tape. Mark the line clearly using a pencil or fine-tip marker. Use a T-square or sturdy straight edge to connect your measurement points with a straight, visible line to guide your scoring on the foam core. Accurate marking here is crucial for neat finishes, especially when working with coolroom panel sheds where dimensional accuracy impacts assembly.
Step 3: Scoring the Panel Face
Secure the panel using clamps or weights to avoid movement during scoring. Using a sharp utility knife, place the blade on the marked line and apply steady pressure, scoring the metal or aluminum faced surface firmly but without forcing the blade through the panel. For coolroom panels Perth WA or any other regional variations, note that a single pass may not be sufficient if the panel is thicker, such as 50mm coolroom panels. Multiple light passes are preferable to avoid tearing the facing material.
Step 4: Completing the Cut Through the Foam Core
Once the surface is scored, gently flex the panel along the scored line if possible. This often helps in snapping through thinner panels. For thicker panels, continue cutting through the foam core within the panel using the utility knife, following the scored face as a guide. Maintain a straight hand and consistent pressure. Avoid sawing motions as they can create uneven edges and damage insulation.
Step 5: Finalizing and Smoothing Edges
After cutting, inspect the edges for any foam or bonding residues. Remove any loose fragments with a fine file or sandpaper to ensure smooth edges, which facilitates better sealing and assembly in your building with coolroom panels project. This finishing step is especially important when using second hand coolroom panels for sale where edges may have uneven wear.
Safely Cutting Metal or Aluminum Faced Coolroom Panels
Composition of Coolroom Panels
Many coolroom panels, including coolroom panels perth and bondor coolroom panels, feature a metal or aluminum facing bonded to an insulating core like EPS. These facings provide durability and protection, but require careful handling during cutting to prevent damage to both the metal skin and insulation. Whether working with a 50mm coolroom panel bunnings stock or 25mm coolroom panels, the key is selecting the right cutting method that ensures clean edges and maintains panel integrity.
Proper Cutting Tools
For metal or aluminum faced coolroom panels, I have found that using power tools equipped with metal cutting capabilities is most effective. A circular saw fitted with a fine-tooth carbide-tipped blade designed specifically for non-ferrous metals works well. Alternatively, a jigsaw with a bi-metal blade or an angle grinder with a cut-off wheel can be used for intricate cuts or adjustments. When working with coolroom panels melbourne or coolroom panels adelaide, sourcing these tools locally is straightforward, especially from specialist suppliers offering coolroom panels for sale and accessories.
Preparing the Workspace and Panel
Securing the coolroom panel on a stable surface is crucial before cutting. Proper support prevents vibration and potential panel damage. I recommend using saw horses or a sturdy bench with clamps to immobilize the panel. When dealing with coolroom panel sheds or larger 50mm coolroom panel for sale materials, ensuring ample space for maneuvering the tools safely is equally important. Wearing appropriate personal protective equipment (PPE) such as gloves, eye protection, and hearing protection is mandatory when cutting metal-faced panels.
Cutting Technique and Panel Protection
Begin by measuring and marking your cut line accurately with a fine-tip marker or scribe, considering any allowances for panel overlaps in your building with coolroom panels. Using a straightedge or guide clamped to the panel ensures a straight, professional cut. When cutting, maintain steady, moderate pressure to prevent chipping or distortion of the metal facing. Scoring the metal gently before running the saw through the full thickness can help produce a cleaner line, especially with eps coolroom panels. Avoid forcing the tool through; let the blade’s speed and sharpness work effectively.
Managing Debris and Heat
Cutting coolroom panelling metal faces generates metal shavings and sparks, particularly with angle grinders. Always clear the workspace frequently to avoid buildup of flammable debris. If possible, perform cuts in a well-ventilated area to dissipate dust and fumes. Additionally, take care to avoid overheating the blade, which can both damage your tools and warp the panel edges. Allow the blade to cool if it starts smoking or glowing red.
Considerations When Purchasing Panels
If you are sourcing materials such as 50mm coolroom panel or exploring options like second hand coolroom panels for sale, factor in the ease of fabricating them with your available tools. Sellers in regions like coolroom panels perth wa or coolroom panels victoria often provide product specifications including recommended cutting techniques, which can be invaluable for a clean and safe cut. Comparing coolroom panels price against usability and quality will aid in making the best choice for your project.
Techniques for Cutting Insulated Sandwich Panels Without Damage
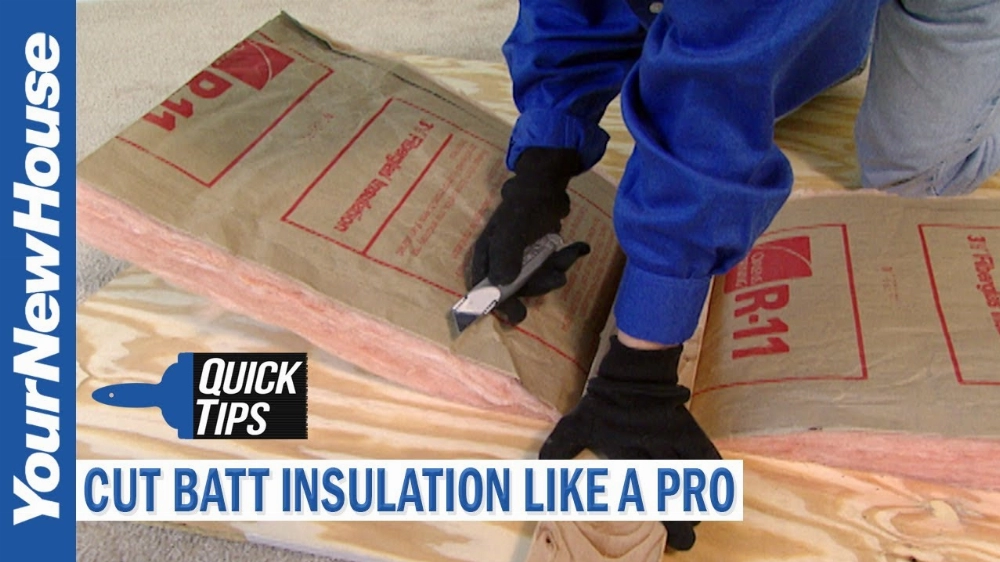
When working with coolroom panels, particularly insulated sandwich panels such as eps coolroom panels or those similar to bondor coolroom panels, precision and care are paramount to maintain their structural integrity and insulation properties. These panels typically consist of an insulating core—often expanded polystyrene (EPS) or polyurethane—sandwiched between metal or aluminium facings. Improper cutting can lead to core damage, delamination, or compromised insulation, which affects the panel’s thermal performance and longevity.
Choosing the Appropriate Cutting Tools
For cutting insulated sandwich panels without damage, selecting the right cutting tool is essential:
Tool Type | Best For | Notes |
---|---|---|
Fine-Toothed Circular Saw | Metal-faced coolroom panels (e.g., 25mm coolroom panels, 50mm coolroom panel bunnings) | Use carbide-tipped blades with at least 60 teeth to minimize chipping. |
Insulation Knife or Hot Wire Cutter | EPS and similar core materials | Ideal for scoring and clean slicing through insulation without dust or debris. |
Jigsaw with Fine Metal-Cutting Blade | Cutting curves or irregular shapes | Use slower speeds and steady feed to avoid burring. |
Utility Knife (for thin panels or scoring) | Scoring and light cuts | Best suited for 25mm coolroom panels or thinner sandwich panels. |
Step-by-Step Cutting Procedure
To reduce the risk of damage when cutting insulated sandwich panels, follow these disciplined steps:
- Measure and Mark Accurately: Use a fine-tip marker and a straight edge for precise cutting lines to avoid rework or jagged edges. When dealing with coolroom panels perth wa or sourcing from other locations like coolroom panels melbourne or coolroom panels adelaide, always verify panel thickness, e.g., 50mm coolroom panel for sale or 25mm coolroom panels, prior to marking.
- Secure the Panel: Support the coolroom panel firmly on a flat, stable surface. Use clamps if necessary to prevent movement that could cause uneven cuts or impact the insulation layer.
- Score the Facing: Lightly score the metal or aluminium facing before full cuts to reduce chipping and edge damage. This step is particularly relevant for bondor coolroom panels and coolroom panel sheds, where precision impacts insulation performance.
- Cuts with Controlled Feed Rates: Use controlled and consistent feed rates when using power tools to minimize vibration and heat generation, which can weaken adhesive bonds in sandwich panels.
- Cut from Both Sides if Necessary: thicker panels like 50mm coolroom panel bunnings options, cutting partially through one side and flipping the panel to finish cuts from the opposite side can help reduce internal core crushing.
Handling Tips to Protect Sandwich Panel Integrity
Handling and supporting coolroom panels properly during cutting not only prevents damage but also reduces wastage and cost overruns:
- Always handle panels by their edges; avoid bending or twisting the panel to prevent delamination.
- Use protective gloves and safety glasses when cutting metal-faced panels to avoid injury from sharp edges or metal shards.
- Work in a clean, dust-free environment to avoid contamination of insulation layers.
Additional Considerations forourcing and Installation
When selecting coolroom panels for sale, consider the following to ensure you receive panels suitable for clean, damage cutting:
Panel Specification | Recommended Cutting Approach |
---|---|
25mm Coolroom Panels | Utility knife scoring and snapping or fine circular saw cuts |
50mm Coolroom Panel | Double-sided cuts with fine-toothed saw, scoring metal facings first |
EPS Core Panels (e.g., Bondor or similar) | Hot wire or insulation knife for clean core cuts without dust |
Sources such as coolroom panels bunnings or suppliers across coolroom panels perth, coolroom panels victoria, and other regions often stock a range of thicknesses and core types. Selecting panels that match your cutting tools and experience reduces errors and saves time during installation.
Handling and Supporting Coolroom Panels During Cutting
Proper Support to Prevent Panel Damage
When working with coolroom panels, especially larger formats like 50mm coolroom panel bunnings or 25mm coolroom panels, providing adequate support during cutting is essential to prevent cracking, bending, or other damage. Panels should be laid flat on a stable, level surface. Using a pair of sturdy sawhorses with additional plywood sheets can create a work platform that distributes weight evenly. This approach is particularly necessary when handling lightweight but rigid panels such as eps coolroom panels or bondor coolroom panels.
Securing Panels to Minimise Movement
Movement during cutting not only compromises accuracy but also increases the risk of damaging the coolroom panel edges or core. To avoid this, clamp the panel firmly but carefully to the work surface. Use soft padding between clamps and panel surfaces to protect the facings, whether metal, aluminum, or other laminates common in coolroom panelling. This is especially relevant when cutting 50mm coolroom panel for sale types or delicate sandwich panels sourced from suppliers like coolroom panels perth wa or coolroom panels melbourne.
Handling Techniques for Different Panel Types
The composition of coolroom panels varies across regions and suppliers such as coolroom panels adelaide or coolroom panels victoria. Lightweight panels with foam cores require careful handling to avoid compromising insulation integrity. When cutting coolroom panel sheds or assembling structures from second hand coolroom panels for sale, gently lifting and supporting panels close to the cut line reduces stress. For heavier sandwich panels, using two or more people to manoeuvre and support the panel edges during cutting operations can significantly improve safety and precision.
Using Proper Cutting Platforms and Guides
Implementing cutting guides or straight edges secured to the panel can help maintain clean, straight cuts while providing additional structural support along the cutting line. This is especially useful when working with coolroom panels perth or coolroom panels price sensitive projects where waste minimisation is a priority. Using platforms specifically designed for building with coolroom panels ensures both the durability of the panels and the accuracy of the cuts.
Environmental Considerations During Handling
Conditions such as wind or uneven ground can make handling exposed coolroom panels difficult on site. When dealing with outdoor environments or temporary setups, take necessary precautions by shielding panels from wind and making sure work surfaces do not have debris or moisture that could damage the panel surfaces or affect cutting accuracy. These precautions apply universally, whether sourcing panels wholesale like coolroom panels bunnings or finding specialty coolroom panels for sale.
Common Mistakes to Avoid When Cutting Coolroom Panels
Inadequate Measurement and Marking
An often overlooked error when working with coolroom panels is rushing through or neglecting precise measurement and marking before cutting. This mistake can lead to inaccurate cuts resulting in poor panel fitment, which affects insulation efficiency and structural integrity. Always use a reliable measuring tape and a straight edge to mark cutting lines clearly. Whether you’re handling 50mm coolroom panels Bunningseps coolroom panels from specialty suppliers, accurate marking ensures your project progresses with minimal waste.
Using the Wrong Cutting Tools
Many fall into the trap of using inappropriate cutting tools for different types of coolroom panels. For example, trying to cut bondor coolroom panels or metal-faced coolroom panels with standard household tools can cause jagged edges or panel damage. Ensure your toolkit is suited to the specific panel type—foam core panels require scoring blades, while metal-faced panels need tin snips or an angle grinder with a suitable disc. Using proper tools also impacts the coolroom panels price by avoiding costly panel replacements.
Poor Panel Support During Cutting
Insufficient support vibrations or panel flex, leading to uneven cuts, delamination, or structural weakening. This is particularly true when working with 25mm coolroom panels or thinner panels, as well with larger insulated sandwich panels commonly used in coolroom panel sheds. Panels should be placed on a flat, stable surface and supported close to the cutting line to prevent bending or chipping.
Ignoring Panel Orientation and Direction
Cutting without considering the orientation of panel’s facings (like aluminum or metal sheets on coolroom panels Perth WA stock) often causes edge flaking or separation. Always cut from the finished side towards the core and apply steady, even pressure. This helps maintain the designed structural layering and avoids compromising the panel’s thermal resistance.
Cutting Without Adequate Safety Measures
Safety negligence is a critical error when cutting any coolroom panels for sale with sharp or power tools. Wear safety glasses, gloves, and a dust mask to prevent injury or inhalation of foam or metal particles. Additionally, ensure the cutting area is ventilated properly, especially when working with EPS or polyurethane panels commonly found across coolroom panels Melbourne and coolroom panels Adelaide markets.
Failing to Account for Panel Thickness and Material Type
Misjudging the panel thickness can result in improper blade selection or cutting technique. For instance, cutting a 50mm coolroom panel for sale using tools intended for 25mm panels can cause tool damage or panel destruction. Consider the panel specification carefully—whether it’s 50mm coolroom panel Bunnings stock or thicker industrial-grade panels—and adjust cutting speeds and tool types accordingly.
Common Mistake | Impact | Recommended Practice |
---|---|---|
Inadequate Measurement and Marking | Incorrect panel dimensions, waste | Use precise measuring tools and mark lines clearly |
Using Wrong Cutting Tools | Jagged edges, panel damage | Match tools to panel materials (foam, metal-faced) |
Poor Panel Support During Cutting | Uneven cuts, delamination | Support panels close to the cut on flat surfaces |
Ignoring Panel Orientation | Facial flaking, layer separation | Cut from finished side inward with steady pressure |
Neglecting Safety Equipment | Injury, respiratory issues | Wear protective gear; ensure good ventilation |
Failing to Account for Thickness | Tool damage, panel waste | Choose tools based on panel thickness and type |
Overlooking Cleanup and Edge Finishing
>Leftover burrs or rough edges from cutting can hinder panel joining and compromise the neatness of building with coolroom panels. Not addressing these imperfections may cause gaps or moisture ingress over time. After cutting, always smooth edges with appropriate abrasives or a file, especially when handling second hand cool panels for sale that may have more delicate or worn facings.
Post-Cutting Tips: Finishing Edges and Preparing Panels for Installation
Ensuring Smooth and Clean Edges
After cutting coolroom panels, it is essential to achieve clean and smooth edges to ensure proper sealing and structural integrity during installation. Edges that are rough or jagged can compromise insulation performance and make panel alignment difficult, particularly when working with 50mm coolroom panels or thinner variants like 25mm coolroom panels. Use a fine-toothed file or sandpaper to gently smooth any irregularities. Take care not to remove too much material, especially when working with eps coolroom panels or panels with metal facings such as bondor coolroom panels.
Sealing Cut Edges to Protect Insulation
Once edges are smooth, it is recommended to apply an appropriate sealant or edge protector compatible with the panel’s materials. This step helps prevent moisture ingress and potential damage to the insulation core, which is critical when building with panels like those commonly available through coolroom panels Bunnings or sourced from suppliers in locations such as coolroom panels Perth WA and coolroom panels Melbourne. The following table summarizes suitable sealing options based on panel types:
Panel Type | Recommended Sealant/Edge Protection | Notes |
---|---|---|
EPS Coolroom Panels | Polyurethane-based sealant or aluminium tape | Prevents moisture intrusion and maintains thermal efficiency |
Metal Faced Panels (e.g., Bondor) | Butyl rubber tape or silicon sealant | Resists corrosion and weather exposure |
Insulated Sandwich Panels | Edge trims or custom metal angle protectors | Enhances mechanical protection during handling |
Aligning and Supporting Panels Before Installation
Proper alignment and support during installation are critical to maintaining the structural and thermal properties of coolroom panelling. Prior to lifting the panels into position, verify that all cut edges match the intended dimensions precisely. Supporting panels on level surfaces will prevent warping—common when handling larger sizes such as 50mm coolroom panel for sale options. Additionally, when working with coolroom panels Adelaide or coolroom panels Victoria, consider local climatic conditions that may influence handling and installation techniques.
Handling Leftover and Offcut Materials
Keep any offcuts or leftover pieces from the cutting process for future repairs or panel adjustments. Second hand coolroom panels for sale can provide useful references for comparing finishes or adapting techniques. Store these offcuts in a dry, flat area to prevent deformation or moisture damage, ensuring their usability as patching materials or templates on site.
Additional Recommendations for Optimizing Installation
- Perform a final inspection of all cut edges for consistency and uniformity, especially if using panels from suppliers like coolroom panels Perth or other regional distributors.
- Utilize manufacturer-recommended fasteners and fixing techniques to avoid compromising the panel’s integrity during installation.
- Keep in mind the coolroom panels price variation when selecting seals and edge finishing materials to balance cost and performance.
- Document panel dimensions and seal types used for maintenance and warranty purposes, particularly when installing a coolroom panel shed or commercial refrigeration space.
By adhering to these post-cutting guidelines, the longevity and efficiency of coolroom panels can be assured—regardless if sourcing 50mm coolroom panel Bunnings stock or specialty panels obtained from regional suppliers. Thorough edge finishing and preparation are cornerstones to successful panel installation and sustained performance.