As an expert in coolroom panel installation, one of the most common questions I encounter is, “can you screw into coolroom panels?” Understanding the types and material composition of these panels is vital before attempting any fixings. This article dives deep into panel varieties, the impact of screwing on insulation and structure, and the best practices to ensure secure and damage-free installation.
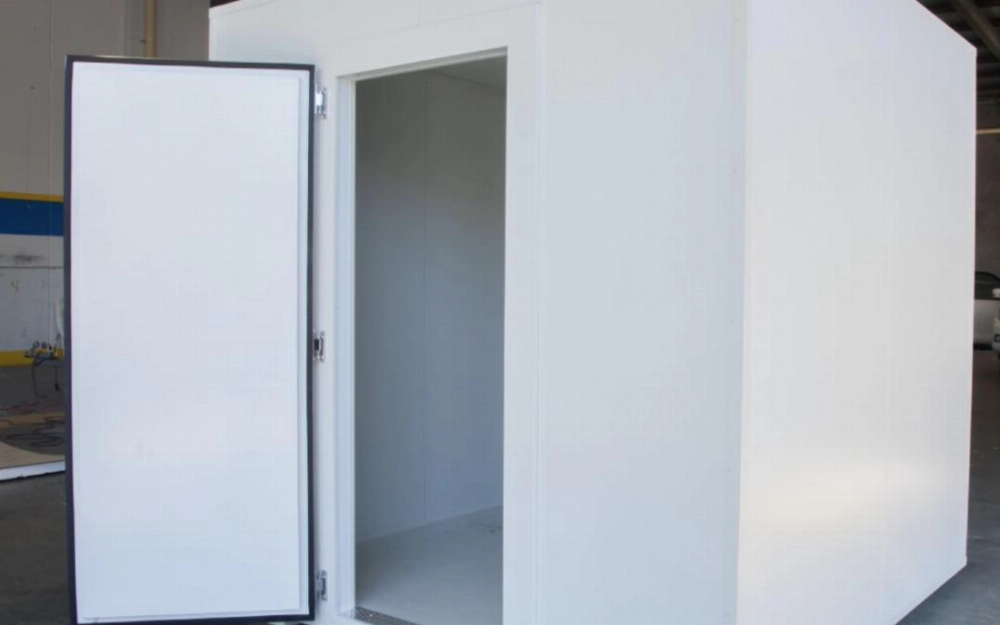
From selecting the right screws to exploring alternative fixture methods that preserve panel integrity, I will guide you through every step—including maintenance tips and common pitfalls. Whether you’re sourcing panels or fixings in Melbourne, Brisbane, or beyond, this comprehensive overview offers the essential insights needed for professional coolroom panel installation and longevity.
Types of Coolroom Panels and Their Material Composition
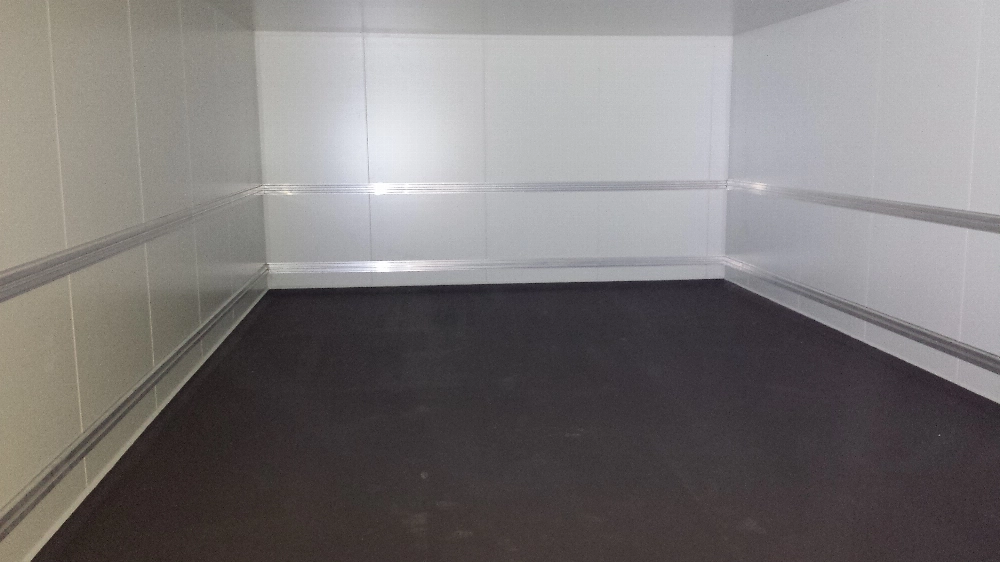
When addressing the question “can you screw into coolroom panels,” it is essential to first understand the various types of coolroom panels and their material composition. The diversity in panel construction directly influences their ability to accommodate coolroom panel fixings such as screws, rivets, or other fastening methods without compromising structural integrity or insulation performance.
1. Sandwich Panels
Sandwich panels are the most common type used in coolroom panel installation across Australia, including regions like Coolroom Panels Melbourne, Brisbane, and Perth. These panels consist of two outer metal sheets—typically galvanized steel or aluminum—and a rigid insulating core. The core materials vary but can include:
Core Material | Description | Usage | Coolroom Panel Thickness (mm) |
---|---|---|---|
Polyurethane (PUR) | Closed-cell foam offering high thermal resistance | Widely used for coolroom panel doors and walls | 50–120 |
Polyisocyanurate (PIR) | Similar to PUR but with better fire resistance | Preferred in regions with stringent fire codes | 50–100 |
Expanded Polystyrene (EPS) | Lightweight and economical foam core | Used in less demanding applications or coolroom panel esky replicas | 50–120 |
The outer metal skins contribute to the panel’s mechanical strength, while the core provides excellent insulation properties. The typical coolroom panel thickness influences the ease of screwing into coolroom panels; thicker panels generally allow for more secure fixings.
2. Foamed-In-Place Coolroom Panels
These panels are created by injecting insulating foam directly between metal facings on-site or during panel manufacture. The in-situ foam expands to fill the cavity completely, ensuring seamless insulation and rigidity. While less common in commercial coolroom builds, this type is sometimes found in coolroom panel homes or custom coolroom panel house applications.
3. Metal Composite Panels (MCP)
In some specialty applications, coolroom panels may be composite metal panels consisting of two metal sheets bonded to an insulating core that is not foam-based, such as mineral wool or other fibrous insulation. These panels offer higher fire resistance and thermal performance but can be more challenging when it comes to installing coolroom panel fixings, requiring careful consideration when choosing screws and installation methods.
Coolroom Panel Accessories Impacting Fixings
Beyond the panels themselves, components like coolroom panel extrusions, coolroom panel joiners, and coolroom panel roofing elements also influence how and where screws can be installed. Extrusions and joiners are often made of aluminum or galvanized steel, providing rigid and stable locations for fixture attachment. Understanding these accessory materials is crucial when planning coolroom panel installation, especially in specialized applications like coolroom panels ballarat or coolroom panels dandenong.
Availability and Sizing
Coolroom panel sizes vary widely depending on the supplier and region, ranging generally from 1.2 meters to 2.4 meters in width and up to 12 meters in length for wall and roof panels. Thicknesses normally fluctuate between 50mm and 120mm, affecting their insulating and mechanical properties.
The market is served by numerous coolroom panel suppliers across Australia with localized availability in areas such as coolroom panels bendigo, bunbury, campbellfield, darwin, geelong, malaga, and major cities. This wide distribution allows customers to source coolroom panels for sale tailored to specific insulation and structural requirements.
Additionally, platforms like coolroom panels eBay and coolroom panels gumtree sometimes offer coolroom panels for sale adelaide, melbourne, perth, and sydney, often at competitive coolroom panel price points, allowing for accessible purchasing options for installers and end-users.
Factors to Consider Before Screwing Into Coolroom Panels
Understanding the Composition and Thickness of Coolroom Panels
Before deciding to screw into coolroom panels, it is essential to identify the specific type and material composition of the panel you are working with. These panels vary significantly in thickness, insulation type, and structural makeup, which directly affect their capacity to hold screws securely without compromising integrity. For instance, coolroom panel thickness plays a crucial role; thinner panels may not sustain heavy loads or frequent screw insertions without risk of damage.
Assessing Panel Components: Doors, Extrusions, and Joiners
Not all areas of a coolroom panel system are suitable for screwing. The presence of coolroom panel doors, coolroom panel extrusions, and coolroom panel joiners must be carefully considered, as these components often include delicate seals or interlocking mechanisms that can be compromised by drilling or screwing. Damaging these elements can affect the panel’s ability to maintain a consistent temperature and airtight environment.
Impact on Insulation and Structural Integrity
Any penetration through a coolroom panel may introduce thermal bridges or create gaps that reduce insulation efficiency. It is important to evaluate how screw holes might affect the foam core or insulation material inside the panels. Moreover, repeated or improper screwing can weaken the structural integrity, leading to potential issues such as panel warping or moisture ingress. These concerns are particularly relevant in applications like coolroom panel homes or industrial coolrooms used in locations including Brisbane, Melbourne, and Bendigo.
Selecting Appropriate Coolroom Panel Fixings
Evaluating the correct type of coolroom panel fixings is a prerequisite prior to installation. Not all fixings are compatible with the range of coolroom panels australia suppliers provide, especially when considering variables in coolroom panel sizes and materials available in regions such as Campbellfield, Dandenong, and Ballarat. Fasteners must be chosen based on the panel’s substrate to avoid corrosion, minimize thermal bridging, and maintain sealing.
Consulting Availability and Regulations from Local Suppliers
Availability and regulations around mechanical fastenings can vary by region. When sourcing panels or coolroom panel installation services, referencing local advice from coolroom panel suppliers in key areas like Adelaide, Perth, Sydney, or Malaga is advisable. This ensures compatibility with the recommended screw types and adherence to any building codes or warranty requirements. Considering local supply options such as coolroom panels for sale Melbourne or coolroom panels near me reduces logistical challenges during installation.
Evaluating Functional Requirements and Load Considerations
Depending on whether the screw installation is for mounting shelving, fixtures, or attaching an external coolroom panel esky, load considerations must be carefully calculated. The screw’s holding power on insulated panels differs markedly from other construction materials. Ensuring that the mechanical load does not exceed what the panel can handle prevents premature panel failure or detachment of installed components.
Recommended Screws and Fasteners for Coolroom Panels
Understanding Material Compatibility
When considering coolroom panel installation, selecting the appropriate screws and fasteners is critical to maintain the integrity of the panels and ensure a secure fit. Most coolroom panels australia are constructed from a sandwich of insulated cores with metal facings, commonly steel or aluminum. Using incompatible fasteners can cause corrosion, reduce insulation performance, or damage panel surfaces. Therefore, fasteners made from stainless steel or other corrosion-resistant materials are generally recommended.
Types of Screws Recommended
For typical applications such as attaching coolroom panel doors or fixing trims and coolroom panel extrusions, the following screw types are preferred:
Screw Type | Material | Head Type | Best Use Case | Recommended Length |
---|---|---|---|---|
Self-tapping screws | Stainless steel or zinc-plated steel | Hex washer or pan head | General panel fixing, including coolroom panel joiners | 25-50 mm (depending on panel thickness) |
Tek screws (self-drilling) | Stainless steel or coated carbon steel | Hex washer head | Attaching metal trims, coolroom panel roofing, and extrusions | 20-40 mm |
Blind rivets | Aluminum or stainless steel | Pull-type rivet | Areas requiring non-intrusive fixing to avoid thermal bridging | N/A (based on rivet size) |
Fastener Characteristics to Prioritize
Because coolroom panels often have a thermal insulation core, it is essential to choose fixings that minimize heat transfer and prevent moisture ingress:
- Corrosion resistance: Fasteners must resist rust, especially in humid environments typical of coolroom panel esky applications.
- Appropriate length: Screws should penetrate enough into the substrate or framing but not cause damage through over-penetration.
- Sealing capability: Use screws with integrated sealing washers or apply compatible sealants to prevent moisture leaks.
- Low thermal transmission: Avoid steel fasteners in direct contact with the panel insulation core for prolonged periods where possible.
Considerations for Specific Applications
In projects ranging from coolroom panel homes to industrial refrigeration units, the requirements for fasteners may vary:
Application | Recommended Fastener | Additional Notes |
---|---|---|
Coolroom panel doors | Stainless steel self-tapping screws with sealing washers | Enhances door alignment and moisture resistance |
Roofing and wall panels (e.g., coolroom panel roofing) | Tek screws with neoprene washers | Prevents water ingress and maintains panel integrity |
Panel joiners and extrusions | Blind rivets or self-tapping screws | Ensures thermal breaks are maintained and mechanical strength |
Sourcing Quality Fasteners
When searching for coolroom panel suppliers or coolroom panels for sale Melbourne and other regions such as coolroom panels Brisbane, coolroom panels Ballarat, or coolroom panels Perth, it is equally important to source quality coolroom panel fixings from reputable providers. Distributors who specialize in refrigeration and insulated panel systems often provide fasteners tested specifically for compatibility with panel thicknesses and materials. Checking specifications for coolroom panel thickness and matching fasteners accordingly ensures the long-term durability of the installation.
Step-by-Step Guide to Safely Screw Into Coolroom Panels
Assessing the Coolroom Panel Type and Location
Before beginning any coolroom panel installation or modification, it is essential to identify the coolroom panel thickness and material composition. Most coolroom panels consist of insulated sandwich panels with an inner core of polyurethane or polystyrene, clad with metal sheeting. The presence of coolroom panel extrusions or joiners can also affect where and how you place your fixings. For example, when working on coolroom panel doors or near coolroom panel roofing sections, ensure the integrity of the seal and insulation is maintained.
Gather the Appropriate Tools and Materials
Using the correct coolroom panel fixings is critical. Choose screws compatible with the panel’s metal skin, typically self-tapping or self-drilling screws with corrosion resistance properties. To avoid compromising the insulation, fasteners should have rubber washers or neoprene seals for airtight installation. Tools required include a drill with adjustable torque settings, appropriate screwdriver bits, a tape measure, a level, and marking tools. If purchasing materials, consider reputable coolroom panel suppliers from your region, such as those offering coolroom panels Melbourne or coolroom panels Brisbane.
Marking Drill Points with Precision
Carefully measure and mark the positions where screws will be placed. Avoid placing fasteners too close to panel edges or seams, especially around critical areas like panels used in coolroom panel homes or coolroom panel houses. Maintaining at least 30mm distance from edges helps preserve structural integrity and prevents cold bridging. Use a level to ensure alignment, especially on vertical panels or when attaching shelving or fixtures to the coolroom panel esky or interior surfaces.
Pre-Drilling and Drilling Techniques
To prevent damage to the panel’s outer metal skin and insulation, it is advisable to pre-drill pilot holes with a drill bit slightly smaller than the screw diameter. This step reduces the risk of panel deformation or cracking. When drilling, maintain steady pressure and use a low-speed setting to avoid overheating the area and compromising panel material. For screw depth, ensure penetration reaches the metal substrate without penetrating too deeply, which could damage insulation or affect the panel’s thermal performance.
Inserting Screws and Securing Fixings
Insert screws carefully, applying consistent torque to tighten without over-tightening, which can deform the panel or break the fastener’s sealing washer. The use of coolroom panel fixings with integrated rubber seals helps maintain airtightness and moisture resistance. Check each screw as you install to confirm it is flush with the panel surface but not overly compressed. This step is especially important when working with coolroom panel joiners or when attaching fixtures that will bear weight or vibration.
Final Inspection and Testing
After installation, inspect the coolroom panel for sale or existing panels for any visible damage or gaps around the screws. Conduct a simple air leak or moisture test if possible, especially in cold storage rooms. Ensuring the panel’s insulation and structural integrity remain intact prevents future issues such as condensation or energy loss. Maintaining proper screw placement and seal integrity aligns with best practices observed by coolroom panels Australia providers and specialists in regions like Ballarat, Bendigo, and Campbellfield.
Common Mistakes to Avoid When Installing Screws in Coolroom Panels
Overlooking the Specificity of Coolroom Panel Materials
One frequent error during coolroom panel installation is assuming all panels respond similarly to screw fixings. Each panel—whether designed for coolroom panel doors, coolroom panel roofing, or wall applications—varies markedly in coolroom panel thickness and core material. Utilizing standard screws rather than those tailored to coolroom panel fixings can compromise the panel’s integrity and insulation. It is critical to source appropriate screws recommended by coolroom panel suppliers to ensure secure and damage-free attachment.
Failing to Account for Panel Extrusions and Joiners
Installing screws without consideration for coolroom panel extrusions and coolroom panel joiners leads to improper fitment and potential leaks or panel distortion. Screwing directly over joiners may weaken the joint or cause misalignment. Attention to the position of extrusions and reinforcing structural parts is necessary to maintain the panel’s performance, especially in coolroom panels Australia where conditions demand high insulation standards.
Inadequate Pre-Drilling or Using Incorrect Screw Sizes
A common mistake is neglecting to pre-drill pilot holes or using screw sizes inconsistent with panel design. Excessively large or long screws penetrate beyond intended limits, damaging internal insulation or leading to moisture ingress. Conversely, undersized screws fail to provide adequate hold. Referencing a detailed sizing chart can help prevent such issues:
Coolroom Panel Thickness (mm) | Recommended Screw Length (mm) | Recommended Screw Diameter (mm) |
---|---|---|
40 | 20-25 | 4.2 |
50 | 25-30 | 4.8 |
75 | 30-35 | 5.0 |
100 | 35-40 | 5.5 |
Ignoring Thermal Expansion and Panel Movement
Coolroom panels undergo expansion and contraction due to temperature changes. Rigidly fixed screws without allowance for this movement can lead to panel warping or screw shear. Incorporating screw fastening techniques that allow slight panel movement, particularly around coolroom panel doors and edging, is essential to prevent premature wear or failure.
Poor Sealing After Screw Installation
Installation without proper sealing of screw holes is a major oversight. Penetrating the coolroom panel esky or internal core without resealing invites moisture infiltration, reducing insulating efficiency and contributing to mold or corrosion. Using appropriate sealants recommended by coolroom panel suppliers and ensuring coverage over screw heads will maintain panel performance and longevity.
Using Incompatible Screw Materials
The wrong screw material can lead to corrosion, especially in high-humidity environments typical for coolrooms. Avoid using standard steel screws; instead, opt for stainless steel or coated screws designed for coolroom panel installation. This consideration is particularly relevant when sourcing coolroom panels Melbourne or from other suppliers across Australia such as coolroom panels Ballarat or coolroom panels Brisbane.
Rushing Installation Without Proper Supporting Structures
Screws must anchor into solid substrates or adequately designed support frameworks. Skipping or underestimating this step often results in loose fixings and panel damage. When installing on surfaces like coolroom panel homes or custom-built coolroom panel houses, reinforcing frames and ensuring compatibility between screws and supporting structures is crucial.
Impact of Screwing on Coolroom Panel Insulation and Structural Integrity
Effect on Insulation Performance
When considering whether you can screw into coolroom panels, it is essential to understand the impact on their insulation properties. Coolroom panels rely heavily on their core insulation material, typically polyurethane foam or polystyrene, to maintain thermal efficiency. Penetrating the panel with screws can create thermal bridges at the point of penetration, leading to localized heat transfer. Over time, this may reduce the overall energy efficiency of the coolroom.
Moreover, improper sealing around coolroom panel fixings can lead to air and moisture ingress, which deteriorates insulation integrity and promotes condensation buildup. This issue can be especially critical in coolroom panel doors and junctions where specific sealing standards are required. Ensuring that all screw penetrations are adequately sealed with appropriate gaskets or sealants mitigates this risk effectively.
Impact on Structural Integrity and Panel Stability
Coolroom panel installation calls for maintaining the structural integrity of the panels, which can be compromised if screws are not selected or installed properly. The panels, including those with coolroom panel extrusions and coolroom panel joiners, are designed to distribute loads evenly across their surfaces. Incorrect screw placement or over-tightening can cause panel deformation or damage to the panel thickness and internal core.
Repeated mechanical stress from loose screws or inappropriate fasteners weakens the connection points and may lead to panel fatigue, jeopardizing the safety and longevity of the coolroom structure. This is particularly notable in larger structures such as coolroom panel homes or extensive coolroom installations found in commercial settings across regions like coolroom panels Melbourne, coolroom panels Brisbane, or coolroom panels Ballarat.
Considerations for Panel Types and Applications
The impact on insulation and structure also varies depending on the coolroom panel sizes and types. For example, coolroom panel roofing experiences different stresses compared to wall panels or coolroom panel esky-type modular units. Different manufacturers and coolroom panel suppliers offer panels with varying core densities and outer skins, which influence how penetrations should be executed.
When sourcing coolroom panels for sale or planning maintenance, it is advisable to consult product-specific guidelines to ensure that any screw installation does not void warranties or reduce performance. Panels designed and supplied in locations like coolroom panels Perth, coolroom panels Adelaide, or coolroom panels Dandenong may have unique installation requirements.
Long-Term Effects and Maintenance Implications
Over time, even minor damage at coolroom panel fixings can propagate if not addressed during the installation phase. This can lead to compromised thermal seals and potential ingress of moisture, accelerating corrosion or damage of metal skins in panels used in environments like coolroom panels Campbellfield or coolroom panels Malaga.
Routine inspection and maintenance after screwing into panels should include checking for seal integrity, tightening or replacing fasteners if necessary, and ensuring that panel surfaces remain smooth and intact. This practice is essential to prolong the lifespan of coolroom panels and uphold the high standard expected from installations across various industries.
Alternative Methods to Secure Fixtures Without Screwing Into Coolroom Panels
When considering coolroom panel installation, it is important to recognize that screwing directly into the panels can compromise their insulation properties and structural integrity. Fortunately, there are several effective alternatives to secure fixtures without penetrating the panel surfaces, preserving both the function and longevity of the coolroom panel system.
Using Coolroom Panel Extrusions and Joiners
Coolroom panel extrusions and coolroom panel joiners provide a robust framework for affixing fixtures. These extrusions are typically aluminum or steel profiles that run along the edges of panels, designed to accept specialized coolroom panel fixings without drilling into the insulated core. By anchoring to these extrusions, fixtures such as shelving or lighting can be securely installed.
Method | Description | Suitable For | Advantages |
---|---|---|---|
Clamp Systems | Mechanical clamps attach fixtures to panel extrusions | Shelving, conduit, pipe supports | No damage to panels; easy adjustment and removal |
Magnetic Mounts | Strong magnets placed on metal extrusions for lightweight fixtures | Signs, wire guides, small equipment | Non-invasive; quick installation |
Adhesive Tapes and Pads | High-strength industrial tapes applied to clean panel surfaces | Lightweight fixtures, decorations | No penetration; moisture resistant options available |
Adhesive Solutions for Coolroom Panels
Specialized industrial adhesives designed for low-temperature environments can secure items to coolroom panel doors or walls without screwing. These adhesives must be selected for compatibility with the panel surface material and tested for durability in cold, humid conditions typical of a coolroom environment.
Examples of suitable adhesives include polyurethane-based and epoxy-based formulations that maintain their bond strength despite temperature fluctuations, which is critical in coolroom panels australia and other regions with active refrigeration systems.
Clamp and Bracket Systems Attached to Structural Frames
Rather than relying on the panels themselves, fixtures can often be fastened to the primary structural frame that supports the coolroom panel roofing and walls. Application of clamps, brackets, or hangers on these frames avoids compromising panels directly and provides superior load-bearing capacity.
This method is common in coolroom panel homes or commercial installations where additional equipment or infrastructure needs to be integrated post-panel installation. It is especially effective in locations such as coolroom panels melbourne, coolroom panels dandenong, and coolroom panels campbellfield, where regional suppliers provide compatible structural elements and fixings.
Utilizing Free-Standing Fixtures and Frames
Where permanent fixtures are not necessary, free-standing racks, shelving units, or mobile cabinets can be employed. These avoid any attachment to the panels themselves, thereby preserving coolroom panel thickness and insulation integrity.
This is particularly useful in flexible environments or temporary setups, such as those involving a coolroom panel esky or portable storage solutions commonly seen in areas serviced by suppliers from coolroom panels bendigo to coolroom panels bunbury.
Summary Table: Alternatives to Screwing Into Coolroom Panels
Alternative Method | Typical Use Cases | Benefits | Considerations |
---|---|---|---|
Panel Extrusions & Joiners | Structural mounting, permanent fixtures | Preserves panel integrity; strong support | Requires compatible panel system |
Adhesive Mounting | Lightweight attachments | No panel penetration; moisture-resistant | Limited load capacity; surface prep needed |
Structural Frame Fastening | Heavy equipment installation | Superior strength; no panel damage | Requires access to framework |
Free-Standing Fixtures | Temporary or adjustable setups | No installation required; portable | Space consumption; stability concerns |
In areas where coolroom panels for sale sydney, coolroom panels geelong, or coolroom panels gumtree listings show prevalence, these non-invasive fixing methods maintain market standards and client expectations for quality and durability. It is always advisable to consult with coolroom panel suppliers local to your region, whether in coolroom panels brisbane, coolroom panels malaga, or coolroom panels darwin, to source appropriate fixings and accessories compatible with the specific panel type and thickness involved.
Maintenance Tips After Installing Screws in Coolroom Panels
Proper maintenance after installing screws in coolroom panels is essential to ensure the longevity and performance of the panel system. Whether you have fitted coolroom panel doors, worked with coolroom panel extrusions, or applied fixings to roofing or walls, careful attention post-installation helps maintain insulation integrity and structural stability.
Regular Inspection of Screw Points
Scheduled inspections play a critical role in identifying early signs of wear or compromise around screw fixings. Pay attention to the following indicators:
Inspection Aspect | What to Look For | Recommended Frequency |
---|---|---|
Panel Surface Around Screws | Check for cracking, peeling, or moisture intrusion | Quarterly |
Fixing Tightness | Ensure screws remain firmly secured without over-tightening | Every 6 months |
Sealant Condition | Inspect sealants or washers for wear or degradation | Annually |
Maintaining Insulation and Structural Integrity
Because inserting screws can potentially compromise the insulation panel’s core, it is important to monitor the effectiveness of insulation at and around screw locations. In particular, coolroom panel thickness and materials vary by supplier, so ensure repairs and replacements use matching specifications to preserve thermal performance.
If any evidence of thermal leaks or moisture ingress is observed, immediate action such as resealing screw sites or replacing damaged sections should be initiated to prevent long-term damage. Use approved coolroom panel fixings that are compatible with the panel material to reduce the chance of corrosion or panel degradation.
Protecting Against Corrosion and Weathering
For external applications like coolroom panel roofing or panels used in coolroom panel houses or coolroom panel homes, corrosion at screw points can be a concern. Maintenance best practices include:
- Using stainless steel or coated screws designed for the panel environment, especially in coastal or humid regions such as coolroom panels Brisbane or coolroom panels Darwin.
- Applying touch-up coatings or sealants recommended by the coolroom panel suppliers after screw installation.
- Ensuring that any replacement screws match the original in terms of size (coolroom panel sizes) and treatment to avoid galvanic corrosion.
Documentation and Record Keeping
Maintain detailed records of coolroom panel installation and maintenance activities, including the locations and types of screws used, dates of installation, and subsequent inspections. This information assists in warranty claims, future repairs, and troubleshooting potential issues associated with there being coolroom panel for sale options or new supplies purchased locally, including from sources such as coolroom panels Melbourne, coolroom panels Ballarat, or coolroom panels Dandenong.
Summary of Key Maintenance Actions
Action | Reason | Recommended Frequency |
---|---|---|
Visual Panel Inspection | Detect damage or moisture infiltration near screws | Quarterly |
Check Screw Tightness | Prevent loosening without damaging panel material | Biannual |
Sealant Replacement | Maintain airtightness and waterproofing | Annually |
Corrosion Protection | Prevent rust on screws and panel surfaces | As needed |
Record Keeping | Ensure traceability of installation details | Ongoing |
By adhering to these maintenance practices, any fixture or fitting secured with screws into coolroom panels can perform reliably over time without undermining the panel’s insulation or structural capabilities. For those sourcing components or additional panels, whether from coolroom panels Gumtree, coolroom panels eBay, or regional suppliers like coolroom panels Bunbury or coolroom panels Campbellfield, selecting compatible materials and employing diligent maintenance ensures optimal results.