Are you wondering, can you render cold room panels to boost their performance or appearance? Choosing the right approach for your cold storage can make all the difference in functionality, hygiene, and durability. As a leader in cold room solutions, Cool Room Master knows that getting this right is key to your business success. With years of industry experience, we’re here to share practical, expert insights that go beyond the basics. In this guide, you’ll discover whether rendering cold room panels is feasible, the best methods to do it, and how to ensure long-lasting results for your walk-in cooler or temperature-controlled storage. Let’s dive in and explore how to elevate your cold room with confidence!
What Are Cold Room Panels
Cold room panels are specialized insulated panels designed to create and maintain temperature-controlled environments, such as walk-in coolers and freezers. They act as the walls, ceilings, and floors of cold rooms, providing effective thermal insulation to keep cold air in and warm air out.
These panels are commonly made from materials like polyurethane (PU), polystyrene (EPS), or polyisocyanurate, sandwiched between metal facings such as aluminum or galvanized steel. This composition ensures both insulation efficiency and structural strength.
Cold room panels are essential in various industries, including food storage, pharmaceuticals, hospitality, and manufacturing. They help preserve perishable products, maintain hygiene standards, and support energy efficiency.
The quality of cold room panels is crucial. High-grade panels offer better insulation, durability, and resistance to moisture and wear, ultimately extending the lifespan of cold storage facilities and protecting valuable goods. For reliable insulated panel options, you can explore products like EPS sandwich panels and insulated roof panels from trusted manufacturers.
Can You Render Cold Room Panels The Short Answer
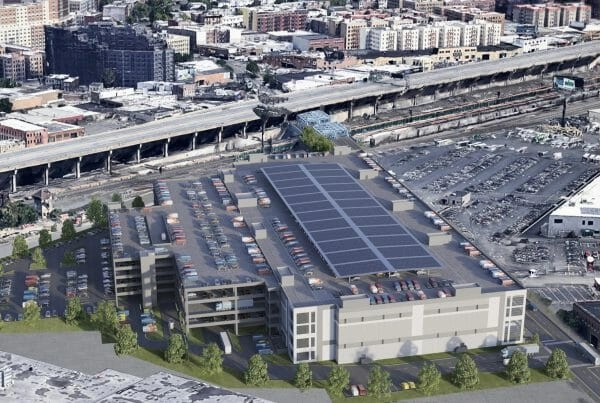
Yes, you can render cold room panels, but it’s not always straightforward. Rendering means applying a coating or finish, like a plaster or specialized paint, over the panels to protect or improve their surface.
The process involves preparing the panel surface, choosing the right rendering material that won’t harm the insulation or structure, and carefully applying it to ensure an even, durable finish.
However, there are a few challenges to keep in mind. Cold room panels are designed for insulation and temperature control, so rendering must not compromise these functions. Moisture, adhesion issues, and maintaining food-safe, hygienic surfaces are major concerns. If the wrong products or methods are used, you can damage the walk-in cooler insulation or reduce panel efficiency.
So, while rendering cold storage panels is possible, it requires the right materials, skills, and attention to industry standards to avoid problems down the line.
Why Render Cold Room Panels Benefits and Use Cases
Rendering cold room panels offers several practical benefits that go beyond just looks. Here’s why it matters:
Aesthetic Improvement for Commercial Spaces
A fresh render gives cold storage panels a clean, uniform appearance. This is especially important in retail environments, restaurants, or food processing plants where customers and inspectors expect a neat, professional look.
Hygiene Benefits for Food Safety and Pharmaceuticals
Rendering creates a smooth, easy-to-clean surface that helps prevent bacteria buildup. For food-safe rendering, this means better protection against contamination, supporting strict hygiene standards required in food processing and pharmaceutical storage.
Durability Protection Against Wear and Moisture
Cold room panels face constant moisture and temperature swings. A good rendering layer acts as an extra barrier, protecting panels from damage, corrosion, and wear—extending their lifespan and reducing maintenance costs.
Insulation Enhancement Advantages
While cold storage panels already insulate well, rendering can boost this property slightly by sealing small gaps or imperfections. This helps maintain consistent temperature control and energy efficiency.
Real-World Examples
- A commercial kitchen in Chicago revamped its walk-in cooler panels with a hygienic, food-safe render, reducing cleaning time and improving compliance during health inspections.
- Pharmaceutical warehouses in California applied specialized coatings on their cold storage panels, enhancing durability in demanding environments.
- Retail grocers in Texas used rendering to refresh insulated panel walls, creating a more pleasant customer space without costly panel replacements.
For United States businesses, rendering cold room panels is a cost-effective way to improve hygiene, durability, and appearance while supporting energy efficiency in temperature-controlled storage.
How to Render Cold Room Panels Step-by-Step Guide
Step 1 Assess Panel Material and Suitability
Before you start, check what your cold storage panels are made of. Most panels use polyurethane or polystyrene insulation with metal skins. Some materials don’t hold render well, so make sure your panels can handle the extra layer without damaging insulation or structure.
Step 2 Surface Preparation
Clean the panels thoroughly. Remove dirt, grease, or loose particles that might stop the render from sticking properly. Light sanding or a primer coat can help, especially on smooth metal surfaces, to give the render a better grip.
Step 3 Choose the Right Rendering Material
Pick a food-safe, moisture-resistant render designed for insulated panel coating. Acrylic or specialized epoxy renders often work best because they handle cold, humidity, and cleaning chemicals common in walk-in cooler insulation.
Step 4 Application Process
Apply the render evenly using a trowel or spray equipment. Start with a thin base layer, let it dry, then add more layers until you get the thickness and finish you need. Take care not to clog panel joints or cam locks, as these are vital to cold room performance.
Step 5 Curing and Testing
Let the render cure fully according to manufacturer instructions — usually a few days. After curing, test for adhesion and check that insulation and sealing still perform well. You want to make sure the rendering hasn’t affected the cold room’s temperature control or hygiene standards.
Challenges and Considerations When Rendering Cold Room Panels
Rendering cold room panels isn’t always straightforward. Here are some key challenges to keep in mind:
Potential Risks of Rendering
- Rendering can sometimes affect the panel’s insulation, reducing its efficiency in temperature-controlled storage.
- Poor surface preparation can lead to peeling or cracking, which harms hygiene standards important in food-safe rendering.
- Applying the wrong materials might cause moisture buildup or corrosion, damaging sandwich insulated panels.
Industry-Specific Requirements
- Food and pharmaceutical industries have strict hygiene rules. Any rendering must meet these standards to ensure hygienic cold storage.
- Some commercial refrigeration panels require coatings that resist chemicals or cleaning agents used regularly in US facilities.
Cost Considerations and Service Options
- Rendering can add extra upfront costs including labor, materials, and downtime during installation.
- You’ll find DIY options, but professional services like Cool Room Master usually offer better quality and long-term value.
- Honest Pricing, Real Quality, Better Service—Cool Room Master specializes in tailored solutions that fit your budget and meet local standards.
When you’re in the US market, picking the right rendering approach is about balancing cost, durability, and industry compliance to keep your cold storage panels performing their best.
Alternatives to Rendering Cold Room Panels
If rendering cold room panels isn’t the best fit for your project, there are solid alternatives to consider:
Pre-finished Ready-to-Use Panels
These panels come with factory-applied coatings and finishes. They save time and ensure consistent quality, offering good insulation and hygienic surfaces without the need for extra rendering. Perfect for quick installation in commercial refrigeration and cold storage setups.
Cladding and Protective Films
Using specialized cladding materials or protective films is another option. These provide an extra layer of protection against moisture, wear, and contamination. Food-safe cladding can enhance hygiene without compromising insulation or temperature control.
Regular Maintenance Practices
Keeping cold room panels in top shape with routine cleaning, inspection, and minor repairs can massively extend their life and performance. Maintaining seal integrity and fixing damage early often reduces the need for costly re-rendering or replacements.
Choosing the right option depends on your cold room’s use, budget, and local conditions—whether you’re upgrading insulation, improving hygiene for food safety, or aiming for durability in busy commercial kitchens or storage facilities.
FAQs About Rendering Cold Room Panels
Can all cold room panels be rendered
Not every cold storage panel is suitable for rendering. Panels made from materials like polyurethane or polystyrene need special care, and some factory-finished insulated panels come with coatings that don’t hold render well. It’s important to check the panel type and consult with the manufacturer before starting.
Does rendering affect insulation performance
If done correctly, rendering shouldn’t hurt the insulation or temperature-controlled storage efficiency. However, poor application or using the wrong render can trap moisture or damage the panel’s surface, which may reduce effectiveness over time.
Is rendering food-safe
Food-safe rendering is a must for commercial refrigeration panels used in food or pharmaceutical storage. You’ll need to pick hygienic, easy-to-clean coatings approved for food environments. Avoid paints or renders that can peel or release harmful substances.
Cost considerations
Rendering cold room panels adds upfront costs, including materials and labor. Professional application usually costs more but can save you from future repairs or performance issues. Consider long-term benefits vs. initial spend.
DIY vs professional rendering
Rendering panels yourself might seem like a budget-friendly option, but cold room maintenance demands high standards for hygiene and insulation. Professionals bring experience with the right materials and techniques, which reduces risks and ensures a longer-lasting finish. For U.S. businesses, hiring local experts familiar with industry standards is often the safer bet.