If you’ve ever wondered, can you paint coolroom panels?
The answer is yes—but it requires careful consideration of panel type, thickness, and material. In this article, I’ll guide you through assessing feasibility, selecting the right paints, and preparing surfaces to achieve a durable, hygienic finish that preserves insulation.
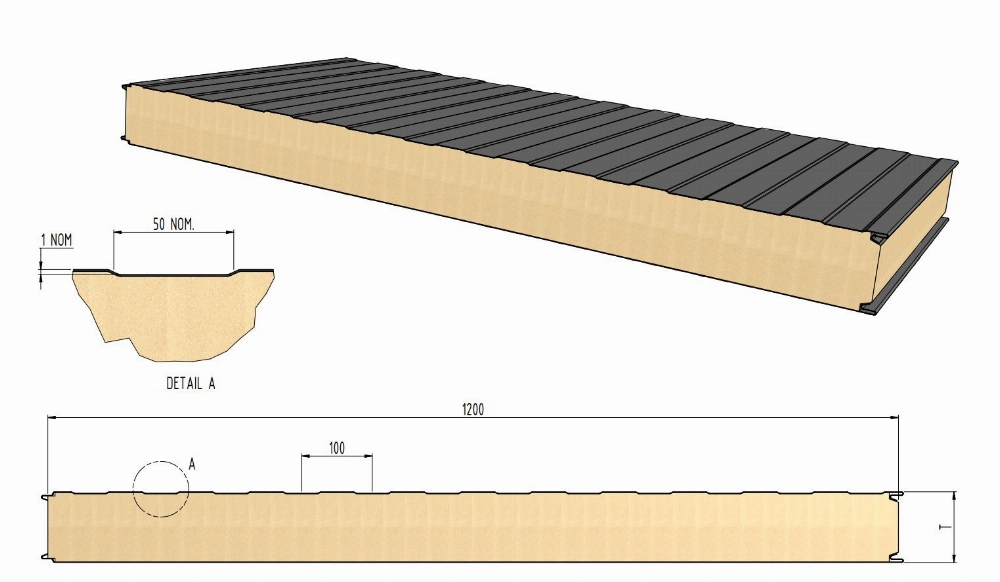
From handling various panel thicknesses
- 25mm
- 50mm EPS Panel
- 75mm
to navigating surface compatibility with brands such as Askin or Austec, this comprehensive guide covers expert tips and common pitfalls. Whether you’re a DIY enthusiast or considering professional services, understanding the nuances behind painting coolroom panels ensures your coolroom remains efficient and visually appealing.
Assessing the Feasibility of Painting Coolroom Panels
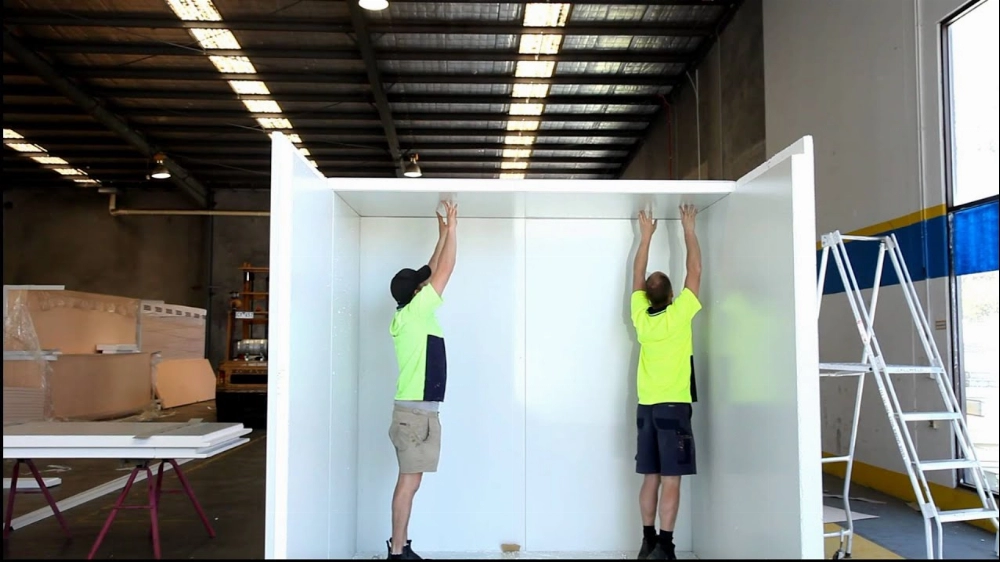
When considering painting coolroom panels, it is essential to assess their suitability for this process to ensure durability, functionality, and maintained insulation properties. Coolroom panels come in various thicknesses and materials, including popular options such as 25mm coolroom panels, 35mm coolroom panels, 50mm coolroom panels, and 75mm coolroom panels. Each of these thicknesses will affect the panel’s structural integrity and response to surface treatments like painting.
Material Composition and Surface Type
Insulated coolroom panels usually consist of an insulating core, often polyurethane or polystyrene foam, sandwiched between metal facings like aluminium or steel. For instance, aluminium coolroom panels are common in both commercial and residential coolrooms. Brands such as Askin coolroom panels, Austec coolroom panels, and Austral coolroom panels, including those sourced from distributors like Australian Coolroom Panels Pty Ltd, generally adhere to these material standards.
The surface to be painted typically includes smooth metal sheeting that requires adequate preparation to promote paint adhesion. It is critical to note that painting over improper surfaces could lead to flaking, reduced hygiene, or compromised panel integrity.
Structural Considerations and Panel Thickness Impact
Panel Thickness | Typical Use | Considerations for Painting |
---|---|---|
25mm Coolroom Panels | Light refrigeration, small cool storage | Thin panels may be more sensitive to environmental changes and require gentle handling during surface prep and painting |
35mm Coolroom Panels | Moderate commercial refrigeration | Balanced strength and insulation; standard painting procedures typically sufficient |
50mm Coolroom Panels | High-demand refrigeration, larger coolrooms | Robust panels; ensure paint does not trap moisture which could impact insulation |
75mm Coolroom Panels | Heavy-duty commercial and industrial use | High thermal performance; painting should avoid compromising existing surface seals |
In regions like Coolroom Panels NZ and Coolroom Panels Sydney, climatic and regulatory factors play a role in selecting products and services for painting coolroom panels. For example, panels designed for specific thermal efficiency or hygiene standards may not be suitable for painting without professional consultation.
Impact on Insulation and Hygiene
One must carefully consider the effect of paint on the thermal insulation characteristics and hygiene of insulated coolroom panels. An improperly applied paint layer can block ventilation points or create moisture traps which degrade insulation performance and promote microbial growth. This is especially relevant for 100mm coolroom panels and thicker panels where the core insulation is critical.
Compatibility of Paint with Coolroom Panel Surfaces
Prior to painting, it is critical to identify the panel surface type: galvanised steel, aluminium, or other metal sheeting. The compatibility of primers and paints with these surfaces directly affects adhesion and longevity. Some panels such as those from AskIn Coolroom Panels or Austec Coolroom Panels may come with factory-applied coatings that require specific paint types or pretreatment to avoid peeling or corrosion.
Considerations Specific to Panel Fabrication and Modification
For those engaged in building a shed from coolroom panels or modifying panels through how to cut coolroom panels techniques, it is important to reassess painted surfaces post-cutting or alteration to maintain protection and hygiene. Edges exposed by cutting may require additional sealing or priming before painting.
Understanding the 50mm coolroom panel weight and mechanical durability also informs whether painted panels can handle operational stresses without cracking or peeling of the paint layers.
Suitable Paint Types for Coolroom Panels
When considering painting coolroom panels, the choice of paint is critical to ensure durability, maintain insulation properties, and uphold hygiene standards. Different types of insulated coolroom panels, such as the commonly used 100mm coolroom panels, 25mm coolroom panel, and thicker variants like 75mm coolroom panels, require coatings compatible with their surface materials and thermal properties.
Types of Paint Compatible with Coolroom Panels
Most coolroom panels NZ and coolroom panels Sydney are constructed with either a metal face, typically aluminium or steel, or composite surfaces designed for thermal insulation. Therefore, the ideal paint must adhere well to metal surfaces and offer resistance to moisture, temperature fluctuations, and microbial growth.
- Epoxy Paints: These provide excellent adhesion to the aluminium coolroom panels or steel substrates often found in asthin coolroom panels or austec coolroom panels. They form a hard, chemical-resistant coating that is especially useful in hygiene-sensitive environments.
- Polyurethane Paints: Known for flexibility and UV resistance, polyurethane paints are effective for outdoor applications or coolrooms exposed to natural light. They maintain gloss and provide a durable finish compatible with australian coolroom panels pty ltd products.
- Powder Coating: While technically not a paint, powder coating is sometimes applied to aluminium coolroom panels for superior finish and longevity. However, this method requires professional application and is more common during the manufacturing process rather than post-installation painting.
Considerations for Surface Type and Thickness
The substrate of the panel impacts paint selection. For example, 25mm coolroom panels bunnings and 50mm coolroom panels tend to have thinner metallic faces and may require less abrasive surface preparation and lighter paints to prevent damaging the insulation core. In contrast, 50mm coolroom panel perth or 50mm coolroom panel weight variants with thicker metallic facings withstand more robust coatings.
Additionally, coolroom panels with composite or polymer faces need paints formulated for plastics or non-metal substrates, ensuring proper adhesion without degrading the panel’s integrity. This is especially important when dealing with panels like 35mm coolroom panels and 100mm coolroom panels, where maintaining insulation efficiency is paramount.
Surface Compatibility and Hygiene
Using the right paint also means choosing options that do not compromise the panel’s hygiene standards, a critical aspect for food storage applications. Paints with antimicrobial additives or smooth finishes that resist dirt accumulation are preferred for building a shed from coolroom panels or outfitting commercial refrigeration units.
Always verify compatibility with suppliers of askin coolroom panels, austec coolroom panels, or austral coolroom panels, as sometimes manufacturers recommend specific coating types or brands to ensure warranty compliance and optimal results.
Surface Preparation Techniques for Optimal Paint Adhesion
Proper surface preparation is crucial when painting coolroom panels to ensure the paint adheres well and endures the demanding environment typical of coolrooms. Whether you are working with insulated coolroom panels of various thicknesses such as 25mm coolroom panels Bunnings, 50mm coolroom panels, or the heavier 75mm coolroom panels, the preparation steps remain consistent to achieve a durable finish.
Cleaning the Surface
Before applying any coating, the surface must be thoroughly cleaned to remove dirt, grease, dust, and any contaminants. For aluminium coolroom panels or panels from brands like Askin coolroom panels or Austec coolroom panels, use a mild detergent solution and a non-abrasive cloth or sponge. Avoid solvents that could damage the panel surface. After washing, rinse with clean water and allow the panels to dry completely.
Removing Existing Coatings and Oxidation
If the panels have old paint or signs of oxidation, these need to be addressed for optimal adhesion. Light sanding with fine-grit sandpaper (around 220 grit) helps to scuff the surface, improving mechanical bonding. When dealing with Australian Coolroom Panels Pty Ltd products or similar, gentle abrasion prevents damage to the panel’s surface while enhancing paint grip.
Addressing Surface Imperfections and Sealing Joints
Inspect for dents, scratches, or joint gaps, especially in systems incorporating varied panel sizes such as 100mm coolroom panels or thinner options like 25mm coolroom panel components. Use a compatible filler or sealant recommended for coolroom environments to maintain insulation properties and hygiene standards. Proper sealing also reduces potential moisture ingress post-painting.
Priming for Better Adhesion
Applying a primer specifically designed for metal or composite surfaces is critical, especially when painting aluminium coolroom panels or metal-faced insulated panels. Primers not only promote adhesion but also act as a barrier to moisture and corrosion. Select a primer compatible with the paint type and environmental conditions of the coolroom.
Surface Preparation Checklist
Preparation Step | Recommended Method | Remarks |
---|---|---|
Cleaning | Mild detergent wash and rinse | Remove dirt, grease, and contaminants |
Surface Deoxidation | Light sanding with fine-grit paper | Enhances paint adhesion |
Surface Repair | Fill dents and seal joints with compatible sealant | Maintains insulation and hygiene |
Priming | Apply metal/composite-specific primer | Prevents corrosion and improves bonding |
Considerations for Panel Handling and Cutting
When preparing to paint, it may be necessary to cut or modify panels. Knowing how to cut coolroom panels cleanly is part of efficient preparation. Whether working with 50mm coolroom panel Perth suppliers or sourcing 50mm coolroom panel weight data, choosing the best way to cut coolroom panels without damaging the insulation core is essential. Use sharp saw blades designed for insulated panels and protect exposed edges after cutting to prevent moisture ingress prior to painting.
Step-by-Step Guide to Painting Coolroom Panels
1. Selecting the Appropriate Panels
Before beginning any work on painting coolroom panels, identify the specific type and thickness of the panels being used, such as 25mm coolroom panels Bunnings or 100mm coolroom panels. The preparation and painting approach can vary depending on the panel’s material, whether it is insulated coolroom panels featuring a polyurethane core, or metallic surfaces like aluminium coolroom panels. Additionally, familiarize yourself with the specific brand and type, such as Askin coolroom panels, Austec coolroom panels, or Australian Coolroom Panels Pty Ltd products to ensure compatibility with paint types.
2. Preparing the Surface
Thorough preparation ensures both the longevity and aesthetic result of the paint. Start by cleaning the panels with a mild detergent to remove grease, dust, and contaminants, which is critical for coolroom panels Sydney environments where hygiene standards are strict. For panels that have been in service, remove any existing loose paint or corrosion with a wire brush or fine sandpaper. When working with 50mm coolroom panels or 75mm coolroom panels, take care not to damage the insulating core during sanding. For optimal adhesion, lightly abrade the surface with 220-grit sandpaper and wipe down with a lint-free cloth dampened with mineral spirits.
3. Masking and Protection
Protect adjoining surfaces and panel edges by applying painter’s tape and drop sheets, particularly if the coolroom panels are part of a larger assembly or structure such as when building a shed from coolroom panels. Proper masking prevents paint bleed and ensures clean lines, which is especially important for commercial installations like those involving 50mm coolroom panel Perth suppliers or 35mm coolroom panels used in tight spaces.
4. Choosing the Primer and Paint
Select a primer compatible with the panel’s surface and intended paint. Epoxy-based primers are preferred for insulated coolroom panels due to their excellent adhesion and chemical resistance. When focusing on durability and hygiene, use high-quality, antimicrobial, and moisture-resistant paints designed for cool environments. Oil-based or specialized acrylic paints formulated for metal and insulated panels deliver the best results. Brands like those used in coolroom panels NZ installations often require specific primers and paints—always refer to supplier guidelines.
5. Application Techniques
Apply primer uniformly using a brush or roller suitable for smooth surfaces. Airless spray application can provide an even finish on large surfaces but requires skill to avoid runs. Allow the primer to dry as recommended, typically 4–6 hours. For the topcoat, apply two thin coats rather than a single thick one to improve adhesion and appearance. When painting complex panel arrangements, such as 50mm coolroom panel weight configurations, ensure that all edges and joints are properly coated to maintain insulation integrity and hygiene.
6. Drying and Curing
Maintain appropriate temperature and humidity controls during drying, crucial in regions like coolroom panels Sydney where environmental factors fluctuate. Adequate curing times must be observed—generally 24 to 48 hours—to achieve a durable and washable finish, important for maintaining the coolroom’s hygiene standards.
7. Post-Painting Inspection and Touch-Ups
Inspect the painted panels for any uneven spots, missed areas, or paint imperfections. Perform touch-ups promptly using the same paint and application technique to ensure consistency. For larger repairs or modifications which may involve how to cut coolroom panels or adjusting panel thickness such as 25mm coolroom panel additions, reseal and repaint the cut edges as needed to protect against moisture ingress.
Common Mistakes to Avoid When Painting Coolroom Panels
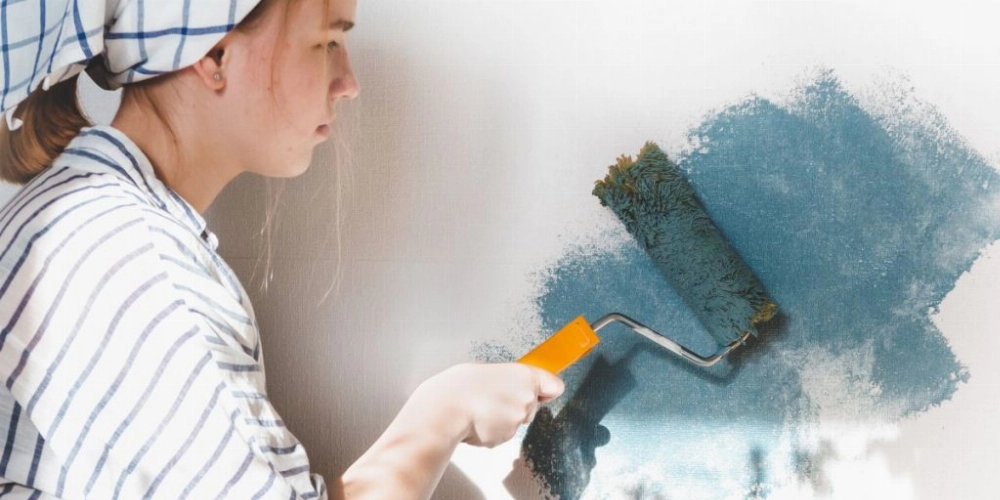
Painting coolroom panels, whether you’re dealing with insulated coolroom panels like 100mm coolroom panels or thinner options such as 25mm coolroom panels bunnings stocks, requires careful attention to detail. Many difficulties can be traced back to avoidable errors during surface preparation, paint selection, or application. Understanding these common pitfalls is essential to achieving a durable finish that does not compromise the panel’s structural integrity or thermal efficiency.
Incorrect Paint Selection
One of the most frequent mistakes is choosing the wrong paint type for coolroom panels. Many people assume that standard interior paints suffice, but painting coolroom panels demands coatings that can withstand cold temperatures, high humidity, and potential condensation. Using unsuitable paints can lead to poor adhesion, peeling, or degradation over time.
Panel Type | Recommended Paint Type | Why |
---|---|---|
Aluminium coolroom panels | Epoxy or polyurethane paints | Provides strong adhesion and resistance to moisture |
Foam insulated coolroom panels | Water-based acrylic paints with antifungal additives | Prevents mold growth and maintains insulation performance |
Metal-faced panels (Askin coolroom panels, Austec coolroom panels, Austral coolroom panels) | Metal primer plus suitable enamel paint | Ensures corrosion protection and adhesion |
Poor Surface Preparation
Failing to adequately prepare the surface before painting is another common error. This includes neglecting to clean the panel surface from dust, oils, or residues, as well as not removing or repairing surface damage. Improper preparation can cause uneven finishes or paint failure.
- Best way to cut coolroom panels should ensure clean, smooth edges free from debris before painting.
- Any scratches or dents in 50mm coolroom panels or other sizes must be repaired to maintain thermal integrity and aesthetic appeal.
- Cleaning with appropriate solvents and lightly sanding metal or aluminum surfaces (e.g., aluminium coolroom panels) improves paint adhesion.
Ignoring Environmental Conditions During Painting
Another mistake is not considering environmental factors such as temperature and humidity while painting. Painting in excessively cold or humid conditions can adversely affect drying times and final coating performance. This is particularly important when handling panels in regions like Coolroom panels Sydney or Coolroom panels NZ, where climate conditions vary.
Overlooking the Impact on Insulation and Hygiene
Some users neglect how painting affects the insulation properties and hygiene of panels. Applying thick or incompatible paint layers can hinder the thermal performance of 50mm coolroom panel Perth or 75mm coolroom panels, thereby increasing energy costs. Furthermore, the paint must be suitable to maintain hygienic conditions, especially for food storage coolrooms.
Common Errors Summary
Mistake | Effect | How to Avoid |
---|---|---|
Using incorrect paint type | Peeling, poor adhesion, reduced lifespan | Select paint formulated for cold, humid environments |
Inadequate surface preparation | Uneven finish, paint failure | Thorough cleaning, sanding, repairing panels before painting |
Painting under unsuitable environmental conditions | Long drying times, blistering, cracking | Paint in recommended temperature and humidity range |
Neglecting impact on insulation and hygiene | Reduced insulation efficiency, bacterial growth | Use thin, compatible coatings with antifungal properties |
Mishandling Panel Types with Unique Requirements
Different brands and specs of panels, such as those from Australian Coolroom Panels Pty Ltd or specialized products like Askin coolroom panels, have unique surface characteristics. Applying a “one-size-fits-all” approach to painting can cause suboptimal outcomes. For example, when building a shed from coolroom panels, using a paint not suited to the panel’s composite nature can cause delamination or warping.
Understanding the specific panel makeup and consulting technical datasheets or manufacturer guidelines is crucial.
Overlooking Weight and Thickness Considerations
When handling and painting various panel sizes like 35mm coolroom panels, 50mm coolroom panels for sale, or the 25mm coolroom panel options, it’s important to recognize how thickness and weight affect installation and finishing techniques. For example, 50mm coolroom panel weight impacts support during painting. Premature handling or moving coated panels before full curing can cause surface damage or paint cracking.
Maintenance Tips for Painted Coolroom Panels
Maintaining the finish of painting coolroom panels is essential to preserve both the appearance and functional integrity of the panels over time. Proper maintenance ensures that the coated surface remains hygienic, durable, and visually appealing, whether the panels are insulated coolroom panels or aluminium coolroom panels.
Regular Cleaning Practices
One of the most important maintenance steps is routine cleaning. Use mild detergents and non-abrasive cloths or sponges to clean painted surfaces. Avoid harsh chemicals that may degrade the paint or underlying material, especially on 25mm coolroom panels Bunnings or larger thickness panels such as 50mm coolroom panels for sale. Frequent cleaning helps prevent the build-up of dirt, mold, or bacteria, important for maintaining hygiene within cold storage environments.
Inspection for Damage and Touch-Ups
Inspect painted panels regularly for any signs of peeling, chipping, or discoloration. This is particularly crucial for panels exposed to frequent usage or movement, such as during building a shed from coolroom panels. Promptly address any damage through spot painting or sanding and repainting affected areas to prevent corrosion or compromised insulation performance. Panels like 75mm coolroom panels or 35mm coolroom panels should be treated carefully to avoid structural damage during such maintenance.
Managing Moisture and Condensation
Coolrooms naturally experience condensation, which can affect painted surfaces if not managed correctly. Ensure the coolroom environment has proper ventilation and humidity control to minimize moisture accumulation on Australian coolroom panels Pty Ltd products or similar brands like Askin coolroom panels and Austec coolroom panels. Excess moisture can lead to paint blistering or mold growth, so regular checks and maintenance of seals and panel joints are recommended.
Protecting Against Physical Impact
Protecting painted coolroom panels Sydney or Coolroom panels NZ from physical impacts maintains the finish and panel integrity. Use protective corner guards or padding in high-traffic areas and during routine activities such as moving stock or installing accessories. For heavier panels, such as the 50mm coolroom panel weight categories, extra caution in handling and impact prevention is necessary.
Repainting Considerations
When the time comes to repaint, ensure the surface is properly prepared by cleaning, sanding, and priming if necessary. Choose paint types compatible with the original coating and the panel material. This applies across thickness varieties from thinner 25mm coolroom panels to bulkier 100mm coolroom panels. Proper repainting not only rejuvenates the panel appearance but can extend the lifespan of the insulation and hygiene benefits.
Impact of Painting on Coolroom Insulation and Hygiene
Effect of Painting on Thermal Insulation
When painting coolroom panels, particularly insulated coolroom panels such as 100mm coolroom panels or thinner options like 25mm coolroom panels from suppliers like Bunnings, it is critical to consider how paint application affects the panel’s thermal performance. Most coolroom panels, whether they are 25mm, 35mm, 50mm coolroom panels, or thicker options like 75mm coolroom panels, rely on their core insulation to maintain temperature control efficiently.
The application of paint introduces a thin additional layer over the existing surface, which generally does not significantly alter the 50mm coolroom panel weight or the thermal conductivity of the panel. However, improper paint selection or excessive paint thickness can potentially clog the panel’s natural breathability or create sites for moisture accumulation, negatively impacting insulation integrity.
For aluminium coolroom panels and other variants supplied by manufacturers such as Askin coolroom panels, Austec coolroom panels, Austral coolroom panels, or Australian Coolroom Panels Pty Ltd, selecting a paint that is compatible with metal substrates and preserves the insulating core is essential. It is advisable to avoid paints that may degrade or soften the panel surface, especially if polyisocyanurate or polyurethane insulation is involved.
Hygiene Considerations After Painting
Casting a new paint layer on coolroom panels can influence hygiene levels within the coolroom environment. Cleanability and resistance to microbial growth are pivotal factors, especially in food storage or processing environments common in regions like Coolroom Panels Sydney or Coolroom Panels NZ markets.
Using antimicrobial or washable paint coatings designed for cold storage applications is highly recommended. These paints assist in maintaining the hygienic quality of coolroom surfaces by providing smooth, non-porous layers that limit bacterial adherence or fungal growth.
Painting coolroom panels without addressing surface preparation can trap dirt or contaminants beneath the paint film, lowering hygiene standards. This is particularly important for panels ranging in thickness such as 25mm coolroom panels or 50mm coolroom panels, where edges and seams require close inspection to ensure thorough treatment.
Recommended Practices and Considerations
Factor | Impact | Best Practice |
---|---|---|
Paint Type | Adhesion, surface protection | Use paints formulated for metal or insulated panel surfaces (e.g., epoxy or polyurethane-based) |
Paint Thickness | Potential insulation alteration | Apply thin, uniform layers to avoid excessive moisture retention |
Surface Preparation | Adhesion and hygiene | Clean and degrease thoroughly; remove contaminants and repair damage |
Panel Type | Paint compatibility | Match paint selection to panel substrate (e.g., aluminium coolroom panels vs. polyurethane foam core panels) |
Panel Thickness | Handling and cutting | Consider best way to cut coolroom panels carefully before painting to avoid damage (reference: building a shed from coolroom panels guidance) |
Conclusion on Painting Coolroom Panels
Overall, painting coolroom panels—whether 35mm coolroom panels, 50mm coolroom panel Perth variants, or other specifications—is feasible without markedly compromising insulation or hygiene when performed correctly. Adhering to proper surface preparation, selecting suitable paint products, and ensuring correct application techniques preserve both the thermal efficiency and hygienic integrity of coolroom environments.
Professional Services vs. DIY Painting for Coolroom Panels
Considerations for Choosing Between Professional and DIY Painting
When it comes to painting coolroom panels, deciding between hiring professional services or undertaking a DIY project depends on several important factors. These include the type of panels involved—whether they are insulated coolroom panels like the common 100mm coolroom panels, thinner 25mm coolroom panels (including options like 25mm coolroom panels Bunnings), or thicker variants such as 75mm coolroom panels—as well as the intended use, location, and the level of finish desired.
Expertise and Equipment
Professional painters possess specialized knowledge of materials such as aluminium coolroom panels, Askin coolroom panels, and industry-standard brands like Austec, Austral, and Australian Coolroom Panels Pty Ltd. They employ appropriate surface preparation techniques and paint types tailored to the panel’s insulation and hygiene requirements. For example, professionals know how to handle variations in 50mm coolroom panel weight or the specific challenges posed by panels sourced from regions like coolroom panels Sydney or 50mm coolroom panel Perth.
DIY Painting: Practicality and Challenges
Undertaking painting yourself can be cost-effective and satisfying, especially for smaller projects or when working with readily accessible panels. However, understanding how to cut coolroom panels correctly and choosing the best way to cut coolroom panels is crucial prior to painting, as poor cutting can affect the paint adherence and overall panel integrity.
Moreover, maintaining panel performance and hygiene standards during DIY projects demands adherence to precise surface preparation and curing processes. Failure to do so can compromise the panel’s insulation properties and hygiene, which is especially critical in food storage or industrial environments.
Comparison Table: Professional Services vs. DIY Painting of Coolroom Panels
Aspect | Professional Services | DIY Painting |
---|---|---|
Expertise in Panel Types | Specialized knowledge of varieties like 100mm, 50mm, 35mm, 25mm coolroom panels | Depends on user research and experience |
Surface Preparation | Advanced techniques ensuring optimal paint adhesion and hygiene | Basic tools and methods, risking inadequate preparation |
Equipment | Access to professional-grade sprayers and drying setups | Limited to consumer-grade brushes and rollers |
Time and Efficiency | Faster turnaround, especially for large-scale projects like building a shed from coolroom panels | More time-consuming; suitable for small or touch-up work |
Cost | Higher upfront cost but with quality assurance | Lower initial expenditure but potential costs due to mistakes |
Impact on Insulation and Hygiene | Minimizes risk of insulation damage or hygiene issues | Greater risk if steps are not followed thoroughly |
Final Recommendations
For projects involving bulk quantities of panels, such as 50mm coolroom panels for sale installations or those located in commercial centers like coolroom panels NZ or coolroom panels Sydney, engaging professional painters ensures compliance with industry standards and longevity of the painted surface.
Conversely, homeowners or small-scale builders working on custom projects—like building a shed from coolroom panels—might opt for DIY approaches, provided they are prepared to invest time into understanding the nuances of how to cut coolroom panels and applying suitable paint treatments.
Ultimately, the choice should weigh the value of professional quality and guaranteed outcomes against the flexibility and cost savings of a DIY painting project.