Exploring EPS and PIR Sandwich Panelling
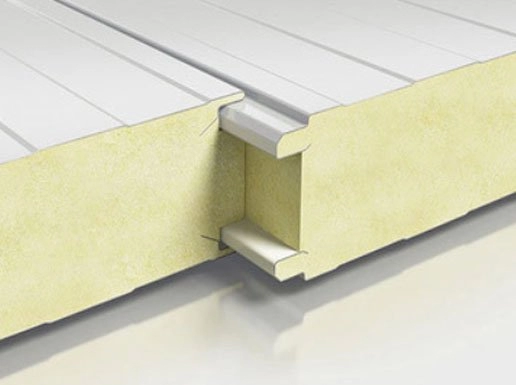
In exploring what is EPS or PIR sandwich panelling, this article delves into the core materials, manufacturing processes, and the distinctive benefits these innovative panels provide. From thermal insulation to fire resistance, understanding these composite panels reveals why they are pivotal in modern construction.
Comparison of EPS and PIR Sandwich Panels
By comparing EPS and PIR sandwich panels in terms of performance, applications, and costs, we uncover how their unique properties influence energy efficiency, safety, and durability. Whether for budget-friendly builds or high-spec projects, knowing the difference guides smarter material choices.
Definition and Composition of EPS and PIR Sandwich Panels
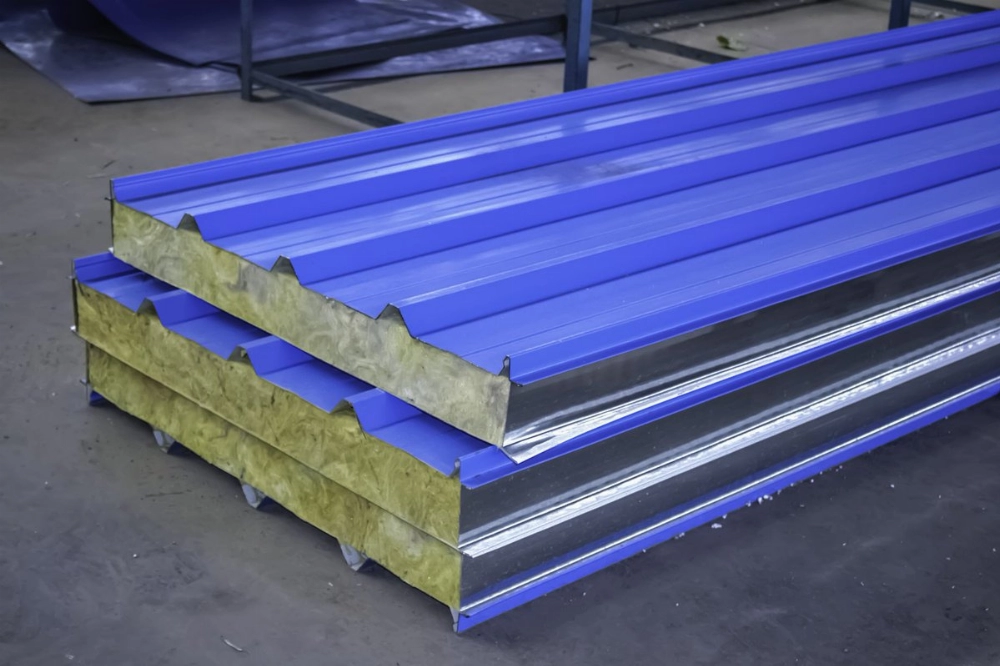
Understanding EPS Sandwich Panels
EPS, or Expanded Polystyrene, is a lightweight, rigid, closed-cell foam material commonly used as the core in sandwich panels. These panels consist of two outer facings—usually made of steel, aluminum, or other durable materials—bonded to the EPS core through an adhesive layer. The EPS core is composed of tiny polystyrene beads that have been expanded and fused together, creating a structure characterized by excellent thermal insulation and reasonable mechanical strength.
Understanding PIR Sandwich Panels
PIR, or Polyisocyanurate, panels feature a core made from a thermoset plastic characterized by a highly cross-linked molecular structure, which enhances rigidity and thermal resistance. Similar to EPS panels, PIR sandwich panels comprise two metal facings bonded to the PIR foam core, delivering superior fire resistance and insulation properties compared to traditional foam cores. The PIR core is produced by reacting polyols and diisocyanates with flame retardants in a controlled process, resulting in a rigid, closed-cell foam with enhanced performance characteristics.
Material Composition Summary
Component | EPS Panels | PIR Panels |
---|---|---|
Core Material | Expanded Polystyrene beads fused into rigid foam | Polyisocyanurate rigid foam with cross-linked structure |
Outer Facings | Steel, Aluminum, or Composite Metals | Steel, Aluminum, or Composite Metals |
Adhesive Layer | Polyurethane or other industrial adhesives | Polyurethane or other industrial adhesives |
Cell Structure | Closed-cell with bead structure | Closed-cell highly cross-linked foam |
Density Range | 15–40 kg/m³ | 30–45 kg/m³ |
Distinctive Characteristics of EPS and PIR Cores
The fundamental differences between EPS and PIR sandwich panels primarily lie in their core composition. EPS is primarily valued for its economic advantages and effective thermal insulation at a lightweight density. However, it has relatively lower fire resistance capabilities. PIR cores bring enhanced thermal performance with improved fire retardant properties due to their chemical composition and cellular structure, making them favorable in applications where higher fire safety standards are required.
Manufacturing Process of EPS and PIR Sandwich Panels
Selection and Preparation of Core Materials
The manufacturing of EPS (Expanded Polystyrene) and PIR (Polyisocyanurate) sandwich panels begins with the careful selection of the core insulation material. For EPS panels, raw polystyrene beads are expanded using steam, forming a lightweight, rigid foam structure. In contrast, PIR panels are produced by mixing polyol and isocyanate chemicals, which react to create a rigid, closed-cell foam with superior thermal properties.
Lamination of Facings
Once the core material is prepared, it is sandwiched between two facings that serve as protective outer layers. These facings are usually made from metals such as galvanized steel, aluminum, or pre-painted steel sheets. During the manufacturing process, these facings are bonded to the core material using specialized adhesives or through chemical bonding methods to ensure structural integrity and durability.
Panel Formation and Pressing
After assembly, the sandwich structure is placed into a pressing unit where heat and pressure are applied. This step is crucial to achieve strong adhesion between the core and the facings, resulting in a uniform panel thickness and enhanced mechanical strength. The pressing process also ensures minimal voids and defects within the core, which could affect insulation performance.
Curing and Cooling
For PIR panels, the curing process allows the foam to fully polymerize and reach its optimal physical properties. EPS panels, on the other hand, may require a cooling phase after expansion before lamination. Controlled curing or cooling ensures the panels maintain their dimensional stability and thermal insulation efficiency during service.
Cutting and Finishing
Once cured, the panels are cut to the required sizes using precision cutting equipment. This stage often includes trimming edges and preparing the panel profiles for installation, such as incorporating tongue-and-groove joints or other locking systems. Additional finishing processes may include applying protective coatings or surface treatments to enhance weather resistance and aesthetics.
Quality Control and Testing
Throughout the manufacturing process, rigorous quality control measures are implemented. These include checks for core density, thermal conductivity, bonding strength, and fire resistance standards compliance. Ensuring consistent adherence to specifications guarantees that both EPS and PIR sandwich panels meet industry requirements for safety and performance.
Thermal Insulation Properties of EPS vs PIR Panels
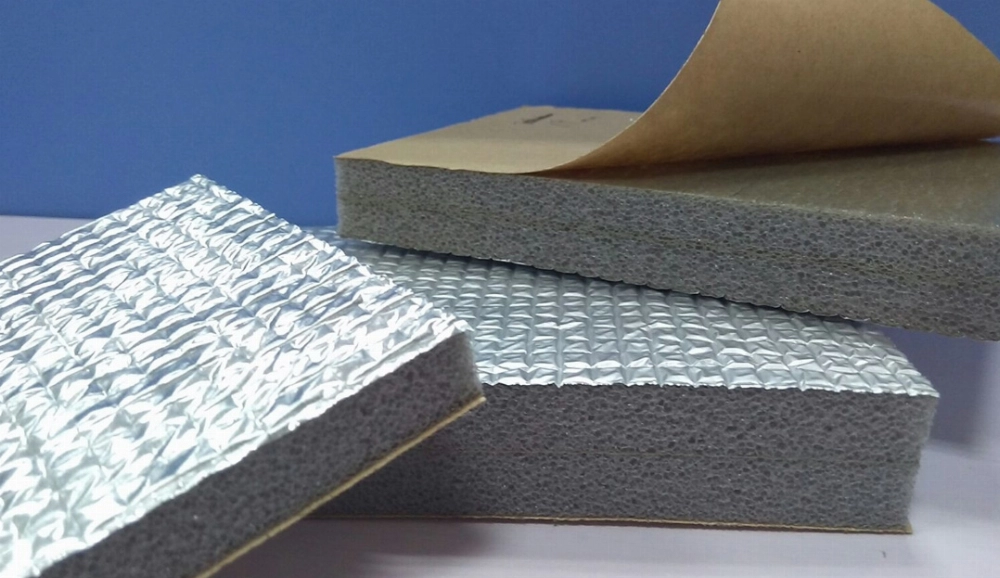
Thermal Conductivity and Insulation Efficiency
EPS (Expanded Polystyrene) and PIR (Polyisocyanurate) sandwich panels differ notably in their thermal insulation performance, primarily due to the inherent properties of their core materials. PIR panels offer a lower thermal conductivity value, typically ranging from 0.022 to 0.028 W/m·K, whereas EPS panels usually exhibit conductivity values around 0.030 to 0.038 W/m·K. This means that PIR panels provide superior insulation per unit thickness compared to EPS, resulting in better energy efficiency in applications where space constraints are a consideration.
Property | EPS Sandwich Panels | PIR Sandwich Panels |
---|---|---|
Thermal Conductivity (W/m·K) | 0.030 – 0.038 | 0.022 – 0.028 |
Thermal Resistance (R-value per 25mm thickness, m²·K/W) | 0.66 – 0.83 | 0.89 – 1.14 |
Impact on Building Energy Efficiency
The enhanced insulation capacity of PIR sandwich panels translates into improved energy conservation for buildings, reducing heating and cooling loads more effectively than EPS panels of equivalent thickness. This is particularly advantageous in regions with extreme climates or stringent energy codes, where maximizing thermal resistance is critical for compliance and operational cost savings.
Effect of Moisture and Aging on Thermal Performance
Both EPS and PIR panels maintain stable thermal properties over time when properly installed; however, moisture ingress can degrade performance. EPS panels are somewhat more susceptible to moisture absorption, which can increase thermal conductivity and reduce insulation effectiveness if protective facings or vapor barriers fail. Meanwhile, PIR panels exhibit lower water absorption rates, maintaining consistent insulation values longer in humid or wet environments.
Thickness Considerations
Due to the difference in thermal conductivity, achieving the same thermal resistance with EPS cores requires thicker panels compared to PIR. For example:
Required Thickness for R-Value 3.0 m²·K/W | EPS Panel Thickness (mm) | PIR Panel Thickness (mm) |
---|---|---|
Approximate Thickness | 90 – 110 | 65 – 80 |
This thickness distinction is a critical factor when considering panel weight, transportation, structural demands, and usable interior space.
Fire Resistance and Safety Features of EPS and PIR Paneling
Fire Performance of EPS Sandwich Panels
EPS (Expanded Polystyrene) sandwich panels consist of a rigid foam core that is known for being lightweight and cost-effective. However, the fire resistance of EPS panels is generally limited unless treated with specific flame retardants. EPS has a tendency to melt and can produce toxic smoke when exposed to high temperatures. Building codes in many regions require additional protective facings or barriers when EPS sandwich panels are used to enhance their fire performance and reduce the risk of ignition and smoke development.
Fire Performance of PIR Sandwich Panels
PIR (Polyisocyanurate) sandwich panels provide superior fire resistance compared to EPS due to their chemical composition and thermal stability. The PIR core contains fire-retardant additives and has a higher melting point, which helps it resist ignition and slow the spread of flames. When exposed to fire, PIR panels tend to char rather than melt, forming a protective carbonaceous layer that acts as an insulating barrier and limits heat transfer. This inherent resistance makes PIR panels a preferred choice for applications where enhanced fire safety is critical.
Fire Safety Standards and Testing
Both EPS and PIR sandwich panels are subject to rigorous fire safety standards and testing protocols worldwide, such as ASTM E84 (Surface Burning Characteristics), EN 13501-1 (Fire Classification of Construction Products), and FM Approval standards. PIR panels often achieve higher ratings in these tests, indicating better flame spread resistance and lower smoke development. EPS panels require careful selection and certification, often being paired with fire-resistant facings or coatings to meet the relevant fire safety criteria.
Smoke Toxicity and Emission Considerations
During combustion, EPS panels can release hazardous gases including carbon monoxide and styrene, which pose significant health risks in enclosed environments. PIR panels emit fewer toxic gases and produce less smoke, contributing to safer evacuation conditions and improved occupant safety in fire incidents. This difference in smoke toxicity is a critical factor in fire safety assessments for construction projects involving sandwich panels.
Additional Safety Features and Protective Measures
To enhance the fire resistance of EPS sandwich panels, manufacturers often incorporate fire-retardant treatments within the foam core or apply fire-resistant facings, such as metal or mineral fiber layers. For PIR panels, additional coatings and aluminum or steel facings are commonly used to maximize fire safety and structural integrity. Furthermore, ensuring proper installation and compliance with fire separation distances and building regulations plays a vital role in mitigating fire risks in structures utilizing these sandwich panels.
Common Applications of EPS and PIR Sandwich Panels in Construction

Overview of Usage
EPS (Expanded Polystyrene) and PIR (Polyisocyanurate) sandwich panels are widely utilized across various sectors of construction due to their excellent insulation properties, structural benefits, and adaptability to multiple environments. Their distinct characteristics allow them to be chosen for specific applications based on project requirements such as thermal performance, fire safety, and durability.
Roofing Systems
Both EPS and PIR sandwich panels are commonly employed in roofing applications where lightweight and high insulation are essential. They provide airtight, waterproof solutions that improve energy efficiency in residential, commercial, and industrial buildings.
Panel Type | Typical Usage | Key Benefits |
---|---|---|
EPS Panels | Cold storage roofs, industrial warehouses | Cost-effective, adequate insulation for moderate climates |
PIR Panels | High-performance roofs, fire-sensitive buildings | Superior insulation, enhanced fire resistance |
Wall Cladding and Facades
Sandwich panels made from EPS and PIR are well-suited for external walls and facades. They offer an effective thermal barrier while also providing structural integrity and weather resistance. In climate zones demanding higher fire safety standards, PIR panels are often preferred due to their improved fire retardant properties.
Cold Storage and Refrigeration
EPS sandwich panels have been a traditional choice for cold storage facilities due to their moisture resistance and good insulating properties at lower costs. However, PIR panels are increasingly adopted where higher thermal resistance and compliance with stringent fire codes are mandatory.
Application | Preferred Panel Type | Rationale |
---|---|---|
Cold Storage Rooms | EPS | Economical insulation with moisture resistance |
High-Safety Refrigerated Facilities | PIR | Enhanced insulation and greater fire resistance |
Industrial and Commercial Buildings
Due to their ease of handling and rapid installation, both sandwich panel types are popular in industrial and commercial building envelopes, including warehouses, factories, and shopping centers. Their strong mechanical properties support cladding systems that also offer significant energy efficiency boosts.
Clean Rooms and Laboratories
PIR sandwich panels are predominantly utilized in clean rooms, laboratories, and other controlled environments due to their non-toxic fire behavior, superior insulation, and ability to maintain stable internal temperature and humidity levels.
Temporary and Modular Structures
Lightweight EPS sandwich panels are often selected for temporary buildings and modular constructions such as site offices, portable clinics, and exhibition spaces. Their ease of transport and assembly aligns well with the requirements of these applications.
Application Area | Panel Type Used | Advantages |
---|---|---|
Clean Rooms / Laboratories | PIR | Fire safety compliance, thermal and moisture control |
Temporary/Modular Buildings | EPS | Lightweight, cost-effective, easy assembly |
Advantages and Disadvantages of Using EPS and PIR Panels
Advantages of EPS Sandwich Panels
EPS (Expanded Polystyrene) panels are widely valued for their excellent thermal insulation properties coupled with lightweight characteristics. One of the primary benefits of using EPS panels is their cost-effectiveness, making them a popular choice for budget-conscious projects without compromising on insulation performance. Additionally, EPS panels offer good dimensional stability and resistance to moisture absorption, which contributes to their durability in various environmental conditions.
Another advantage is the ease of installation due to their light weight and structural simplicity, which can reduce labor time and associated costs. EPS materials are also recyclable, adding an environmental benefit to their profile. However, in terms of fire performance, EPS panels are combustible unless treated with flame retardants, which may influence their selection based on project safety requirements.
Disadvantages of EPS Sandwich Panels
Despite these advantages, there are limitations inherent to EPS panels. Their fire resistance is generally lower compared to PIR panels, which can restrict their usage in applications demanding higher fire safety standards. EPS is also less rigid than PIR, which may impact its suitability in installations requiring higher structural strength or load-bearing capacity.
Additionally, prolonged exposure to UV light can degrade EPS panels if not properly protected, necessitating additional cladding or coatings. Moisture ingress, although limited, can occur through poor seals or damage, potentially reducing the insulating effectiveness over time.
Advantages of PIR Sandwich Panels
PIR (Polyisocyanurate) panels are renowned for superior thermal insulation performance due to their closed-cell structure, providing higher R-values per inch compared to EPS. This makes PIR panels ideal in scenarios where enhanced energy efficiency is a priority or where space constraints demand thinner insulation layers.
From a safety perspective, PIR panels outperform EPS in fire resistance, exhibiting self-extinguishing properties and lower smoke emission during combustion. This characteristic makes PIR panels highly suitable for use in buildings with stringent fire codes and regulations. Structurally, PIR panels possess greater rigidity and compressive strength, offering improved durability and mechanical resilience.
Disadvantages of PIR Sandwich Panels
The main drawbacks of PIR panels include a higher initial cost relative to EPS, which may affect budget planning for large-scale projects. Furthermore, PIR panels are typically heavier and less flexible than EPS, which might complicate handling and installation in certain applications.
In some cases, the manufacturing process of PIR panels involves chemicals that raise environmental concerns, though advancements in technology have reduced their ecological footprint. Additionally, PIR panels are sensitive to moisture, and if core intrusion occurs, it can significantly degrade their thermal and structural performance.
Installation Techniques and Best Practices for Sandwich Panels
Site Preparation and Handling
Proper site preparation is crucial before installing EPS or PIR sandwich panelling. The substructure must be level, clean, and free from debris to ensure uniform panel placement and secure fastening. Panels should be handled carefully using appropriate lifting equipment to avoid damage to the facings and core insulation.
Panel Layout and Alignment
Maintaining accurate alignment during installation impacts both performance and aesthetics. Panels should be positioned in a staggered or modular layout according to design specifications. It is essential to check horizontal and vertical alignment continuously using spirit levels or laser tools.
Fixing Methods and Fasteners
Selection of the correct fasteners depends on the substrate material and panel thickness. Typically, self-drilling screws with neoprene washers are used to prevent water ingress. The table below summarizes common fixing methods:
Substrate Type | Recommended Fastener | Fastening Location | Torque Considerations |
---|---|---|---|
Steel Frame | Self-drilling metal screws with sealing washers | Through panel facings into purlins | Moderate torque to avoid core compression |
Concrete | Expansion anchors or sleeve anchors | Panel edges and mid-span points | Torque per manufacturer guidelines |
Timber Frame | Timber screws with sealing washers | Along framing members | Lower torque to prevent splitting |
Sealing and Jointing
Sealing joints effectively is vital to maximize thermal efficiency and weather resistance of EPS or PIR sandwich panels. Use compatible vapor barriers and high-quality sealants designed for sandwich panel systems. Overlapping tongue-and-groove joints are common and should be sealed with foam or tape specifically formulated for the panel type.
Cutting and Modifications On-Site
When modifications such as cutting or drilling are needed on-site, they should be performed with care to maintain the integrity of the insulation core and facings. Use fine-toothed saws for cutting and avoid excessive heat generation that could affect PIR cores. After modifications, reseal edges with protective coatings.
Fastening and Support Spacing Recommendations
Correct support spacing prevents panel sagging, which can compromise insulation and damage facings. The table below provides typical support center distances for panels based on thickness and type:
Panel Thickness (mm) | EPS Support Spacing (mm) | PIR Support Spacing (mm) |
---|---|---|
50 | 600 | 800 |
75 | 800 | 1000 |
100 | 1000 | 1200 |
Safety Considerations During Installation
Personal protection is important when installing sandwich panels. Appropriate gloves, eye protection, and respiratory masks should be worn to safeguard against dust and sharp edges. Additionally, follow fire safety protocols when working with PIR panels, as they have specific handling requirements due to their chemical composition.
Environmental and Weather Considerations
Installation should ideally occur in dry conditions to prevent moisture ingress before sealing. Panels should be stored upright and covered on-site to minimize exposure to direct sunlight and rain, which can degrade facings and cores.
Cost Comparison and Long-Term Benefits of EPS and PIR Paneling
Initial Cost Analysis
The initial investment for EPS (Expanded Polystyrene) sandwich panels typically tends to be lower compared to PIR (Polyisocyanurate) panels. This cost difference is primarily due to the raw material expense and the complexity of the manufacturing process. EPS panels are generally more affordable, making them a popular choice for budget-conscious projects.
Panel Type | Approximate Initial Cost (per m2) |
---|---|
EPS Sandwich Panels | $15 – $25 |
PIR Sandwich Panels | $25 – $40 |
Long-Term Energy Savings
One of the key long-term benefits of both EPS and PIR sandwich paneling lies in their excellent thermal insulation properties, which reduce heating and cooling costs. However, PIR panels offer a superior thermal resistance (R-value), resulting in better energy efficiency over time even if the initial cost is higher.
Panel Type | Thermal Conductivity (W/m·K) | Approximate R-Value per inch (ft²·°F·hr/BTU) |
---|---|---|
EPS Panel | 0.032 – 0.038 | 3.6 – 4.0 |
PIR Panel | 0.022 – 0.028 | 5.6 – 8.0 |
Because PIR panels provide better insulation, buildings insulated with PIR panels often experience lower utility bills and reduced carbon footprints, which can lead to significant savings over time.
Durability and Maintenance Costs
Both EPS and PIR panels boast durable construction, but PIR exhibits enhanced resistance against moisture, chemicals, and higher temperatures, translating to potentially lower maintenance and replacement costs in demanding environments. EPS panels, while robust, can be more susceptible to water absorption if not properly sealed, potentially increasing maintenance needs.
Lifespan Considerations
When evaluating long-term benefits, the lifespan of sandwich panels directly affects overall cost-efficiency. PIR panels typically have a lifespan of 25-30 years, while EPS panels may last between 20-25 years under comparable conditions. The extended lifespan of PIR panels can justify the higher initial cost in many applications.
Summary of Cost and Benefits
Aspect | EPS Panels | PIR Panels |
---|---|---|
Initial Cost | Lower ($15 – $25/m²) | Higher ($25 – $40/m²) |
Thermal Efficiency | Good (R-Value 3.6 – 4.0) | Excellent (R-Value 5.6 – 8.0) |
Maintenance Cost | Moderate | Lower |
Lifespan | 20 – 25 years | 25 – 30 years |
Energy Savings | Significant | Higher |
Conclusion
While EPS sandwich panels are cost-effective upfront and suitable for many applications, PIR panels offer superior thermal performance, enhanced durability, and longer lifespan, which can translate to greater long-term financial benefits. The decision between EPS and PIR paneling should consider the specific project requirements, environmental conditions, and intended lifecycle to maximize both cost-efficiency and performance.