How to Run Wires Through EPS Panels
Embarking on the task of how to run wires through EPS panels demands precision, planning, and the right tools. In this article, I share essential insights—from selecting proper cutting instruments and mapping wiring routes, to securing cables safely within the foam boards. You’ll learn how to maintain panel integrity while ensuring electrical safety and insulation performance.
Understanding the nuances of embedding wiring inside EPS panels not only protects your installation from moisture and thermal issues but also prevents common mistakes that could compromise safety or efficiency. Join me as I unveil best practices, testing protocols, and expert tips that make running wires through EPS panels a seamless and reliable process.
Tools and Materials Needed for Running Wires Through EPS Panels
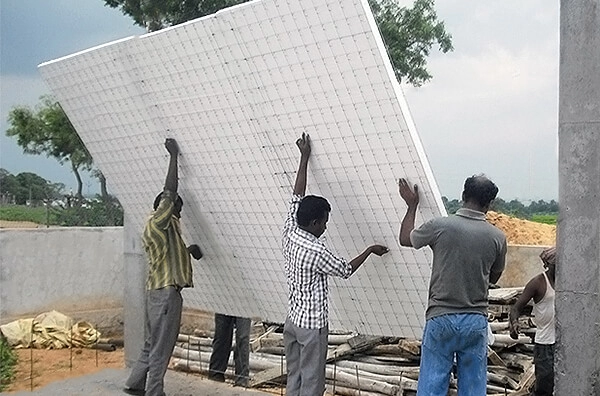
When it comes to running wires through EPS panels, having the right tools and materials on hand is crucial for a safe and efficient installation. In my experience, proper preparation not only saves time but also ensures the integrity of both the electrical system and the insulation panels.
Essential Tools
Tool | Purpose | Notes |
---|---|---|
Utility Knife or Hot Wire Cutter | Cutting channels or grooves in the EPS panels | A hot wire cutter provides cleaner, more precise cuts with less dust |
Fish Tape or Wire Puller | Pulling electrical wires through pre-cut channels or conduit | Ensures minimal force on wires to avoid damage |
Measuring Tape | Measuring routing paths and panel sections | Accuracy here minimizes panel damage and wire strain |
Marker or Pencil | Marking cut lines and wire routes on panels | Use fine tips to avoid excessive marking that could interfere with finishes |
Protective Gloves | Hand protection while cutting and handling panels and wiring | Recommended to prevent injuries and maintain grip |
Drill with Hole Saw or Spade Bit | Creating access holes through EPS panels as needed | Use appropriately sized bits to limit damage to insulation properties |
Recommended Materials
Material | Purpose | Details |
---|---|---|
Electrical Wire | Conductors for power or communication | Select wire types rated for the environment and load, e.g., THHN or UF cable |
Conduit (PVC or Flexible) | Protecting wires within EPS panels | Provides mechanical protection and facilitates wire replacement |
Wire Clips or Staples | Securing wires inside channels | Use plastic or insulated clips to prevent wire damage |
Foam Sealant or Expanding Foam | Sealing cut channels after wiring installation | Ensures thermal continuity and prevents moisture ingress |
Electrical Tape or Heat Shrink Tubing | Protecting wire splices and connections | Essential for insulation and mechanical protection |
Additional Considerations
Depending on the project specifics, I often recommend including moisture barriers or vapor retarders compatible with EPS to maintain insulation performance. Also, selecting low-smoke, halogen-free wire insulation can improve fire safety, which is an important consideration when embedding wiring in foam insulation.
To summarize, careful selection and preparation of these tools and materials streamline the process of running wires through EPS panels while preserving the structural and insulation qualities of the panels.
Planning the Wiring Route Within EPS Panels
Assessing Panel Layout and Structural Constraints
Before beginning to run wires through EPS panels, it is essential to carefully examine the panel layout and any structural elements that may influence the wiring path. This includes identifying the thickness of the panels, locating studs or framing components embedded within or supporting the panels, and understanding any areas designated for insulation or vapor barriers. Planning around these factors helps ensure that the wiring route is feasible and avoids compromising the integrity of the panels.
Mapping the Wiring Path for Efficiency and Safety
Determining the most direct and efficient path for wires within the EPS panels can reduce material waste and prevent unnecessary cutting or modifications to the panels. The route should minimize sharp bends or excessive lengths, as these can affect signal quality or electrical performance. Additionally, the wiring should maintain a safe distance from heat sources, mechanical fasteners, or any potential sources of damage.
Coordinating with Electrical Codes and Regulations
Compliance with local electrical codes and standards is paramount. When planning the wiring within EPS panels, routes must adhere to regulations regarding spacing, conduit installation, and wire protection. For example, certain codes may require the use of conduit or protective sleeves when wires are embedded in foam panels to prevent damage or fire hazards.
Allocating Space for Future Modifications or Additions
It is prudent to anticipate potential future electrical needs by allocating extra space or leaving accessible channels within the EPS panels. This foresight allows for easier upgrades or additions without extensive rework or damage to the existing insulation panels.
Documenting the Wiring Plan
Creating a detailed schematic or diagram of the planned wiring route within the EPS panels supports clear communication with installation teams and inspectors. Documentation should include wire paths, junction points, and any special installation notes to ensure consistency and reduce errors during execution.
Techniques for Cutting Channels in EPS Panels Safely
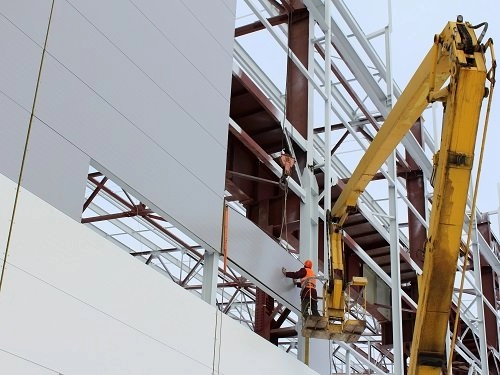
Choosing the Right Cutting Tools
When cutting channels in EPS panels to accommodate wiring, selecting appropriate tools is critical. Common tools include:
Tool | Description | Benefits |
---|---|---|
Hot Wire Cutter | Uses a heated wire to slice through EPS smoothly. | Minimal dust, clean edges, reduces panel damage. |
Utility Knife | Manual tool for scoring and cutting thin channels. | Low cost, precise control for shallow cuts. |
Reciprocating Saw with Fine Blade | Power tool for deeper or longer channels. | Faster cuts for larger jobs when handled carefully. |
Oscillating Multi-Tool | Provides controlled and detailed cutting in EPS. | Good for precise routing with reduced damage. |
Each tool should be chosen based on channel depth, length, and workspace constraints.
Marking and Measuring Channel Paths
Prior to cutting, it is essential to clearly mark wire routes on the EPS panels using a pencil or non-permanent marker. This ensures accuracy and minimizes unnecessary panel modifications.
- Measure the diameter of the wiring bundle plus additional clearance for insulation and conduit if used.
- Mark straight or curved paths depending on wiring plans, maintaining at least 1 inch of material thickness on either side of the channel for panel integrity.
Cutting Methods and Safety Precautions
When performing cuts:
- Make multiple shallow passes rather than one deep cut to avoid cracking or collapsing the EPS.
- Keep the cutting tool perpendicular to the panel surface for a clean channel.
- Avoid excessive force which can crumple or compress the foam.
Additional safety measures include:
- Wearing protective eyewear and a dust mask to protect against EPS particles.
- Conducting cuts in well-ventilated areas to dissipate fumes from heated tools.
- Ensuring power tools are in good working condition and used according to manufacturer instructions.
Maintaining Structural Integrity
Maintaining the strength and thermal performance of EPS panels is paramount. To do so:
- Restrict channel width to the minimum necessary for wiring to avoid weakening panel structure.
- Leave intact EPS around the channel to preserve insulation properties.
- Seal channels after wiring installation with compatible foam or caulking to prevent air infiltration and moisture ingress.
Summary of Cutting Technique Steps
Step | Action |
---|---|
1 | Measure and mark the exact wiring path on EPS panel. |
2 | Select proper cutting tool based on channel dimensions. |
3 | Wear safety equipment: eyewear, gloves, dust mask. |
4 | Cut carefully along marked paths using multiple shallow passes. |
5 | Remove cut EPS debris carefully to avoid compression damage. |
6 | Clean channel and prepare for wire installation. |
Best Practices for Protecting Electrical Wires Inside EPS Panels
Use of Conduits or Protective Sleeves
When running wires through EPS panels, it is essential to encase them within rigid or flexible conduits to provide mechanical protection. This minimizes the risk of abrasion or puncture caused by the rigid foam or during further panel handling and installation. Conduits also facilitate future wire replacement or upgrades without damaging the panel structure.
Maintaining Proper Clearance From Panel Surfaces
Wires should be positioned at a sufficient distance from the outer surfaces of EPS panels to avoid accidental damage from external impacts or fastening operations such as drywall installation. Embedding wiring too close to the surface can lead to insulation breaches or reduced thermal performance of the panel.
Use of Fire-Resistant Materials
Whenever possible, select wires and protective conduits that comply with relevant fire safety codes. EPS is combustible; therefore, incorporating fire-retardant conduits and cables with appropriate insulation ratings is critical to enhancing overall safety.
Securing Wires Within Cut Channels
After creating channels in the EPS panels for wiring, it is advisable to fix wires firmly in place using clips, cable ties, or adhesive strips designed for foam materials. This prevents wire movement that could cause wear and tear, while ensuring that wires do not sag or shift during subsequent panel finishing.
Sealing Entry and Exit Points
To protect wires and maintain panel integrity where cables enter or exit EPS panels, apply appropriate sealants such as fire-resistant foams or caulks. This prevents moisture ingress as well as air leakage, both of which can compromise the thermal and structural properties of the panels.
Accounting for Thermal Expansion
EPS panels expand and contract slightly with temperature fluctuations. Wiring installations must allow for this movement by avoiding overly tight fixation and providing some slack within the protected conduit or sleeve. This reduces strain on wire connections and insulation over time.
Methods for Securing Wires to Prevent Movement or Damage
Understanding the Importance of Wire Securing
When running wires through EPS panels, ensuring that cables remain stationary and protected is crucial to maintaining both the electrical integrity and the structural health of the insulation system. Unsecured wires are prone to damage from vibration, thermal expansion, or accidental impact, which can cause shorts, signal loss, or premature failure.
Recommended Fastening Techniques
There are several effective methods to secure wires within EPS panels safely and reliably:
Method | Description | Key Advantages | Considerations |
---|---|---|---|
Plastic Cable Ties | Use of UV-resistant, non-metallic cable ties to bundle and fix cables along the routed channel. | Cost-effective, easy to install, and prevents wire displacement. | Must be snug but not overtightened to avoid wire damage. |
Adhesive Cable Clips | Small clips with adhesive backing applied directly to EPS surface to hold wires in place. | No penetration into EPS panel; preserves insulation integrity. | Adhesive compatibility with EPS must be confirmed; limited load-bearing capacity. |
Strapping with Insulation-Friendly staples | Special low-profile staples designed to fasten cables without crushing EPS material. | Secure hold with minimal panel damage. | Use with caution to avoid puncturing wires or compressing EPS excessively. |
Wire Mold or Raceway Systems | Installing protective channels or raceways fixed externally along EPS where wires run. | Enhances protection and ease of future access. | Requires additional space and proper anchoring to panel framing. |
Additional Practices for Wire Stability
Beyond fasteners and clips, adopting the following practices significantly enhances wire security:
- Pre-route wires to avoid sharp bends that can lead to wire fatigue or damage.
- Ensure wires are loosely placed within channels to allow for thermal expansion without stress.
- Use chamfered edges or protective sheaths inside cut channels to minimize wear from panel edges.
- When possible, run wires alongside reinforcing elements or framing to enhance fixed positioning.
Material Compatibility and Long-Term Considerations
All securing materials should be compatible with EPS panels and electrical codes. Avoid metal fasteners that risk corroding or damaging wires, and select UV and moisture-resistant options when panels are exposed to environmental conditions. Regular inspection post-installation helps identify any movement or wear early, safeguarding system longevity.
Addressing Thermal and Moisture Considerations When Wiring EPS Panels
Thermal Properties and Wire Heat Management
Expanded Polystyrene (EPS) panels possess excellent insulating capabilities, but this also means that any heat generated by electrical wires embedded within them needs careful management. Electrical wires produce heat based on current load, and without proper ventilation or allowance for heat dissipation, there is a risk of overheating. This necessitates selecting wires rated for higher temperatures or using conduits that provide some air gap between the wire and EPS material. Additionally, spacing wiring channels so that cables do not cluster excessively helps to minimize thermal buildup inside the panels.
Moisture Resistance and Avoiding Condensation
While EPS panels are inherently moisture resistant, one must remain vigilant to prevent any moisture accumulation around wiring areas. Moisture ingress can degrade wire insulation or cause corrosion on metallic conductors over time. It is essential to maintain the integrity of the vapor barrier on the EPS panels when cutting channels for wires. Sealing all penetrations with appropriate foam sealants or vapor-resistant tapes ensures that moisture cannot infiltrate the wiring cavity. Moreover, ensuring that wires have moisture-resistant insulation, such as THWN or UF cables, adds an extra layer of protection against humidity or incidental water exposure.
Preventing Thermal Bridging and Insulation Disruption
Cutting channels for wiring may interrupt the continuous insulation properties of EPS panels, potentially leading to thermal bridging. To mitigate this, channels should be as narrow and shallow as possible while still accommodating the necessary wiring. Backfilling cutouts with compatible EPS or spray foam insulation after wires are secured restores the panel’s insulating capacity. Maintaining continuous insulation around wiring pathways not only preserves energy efficiency but also helps prevent localized condensation caused by temperature differentials.
Use of Protective Conduits and Sleeves
Installing electrical wires inside protective conduits within EPS panels serves multiple purposes: it physically protects wires from compression or damage, facilitates wire replacement or upgrades, and helps manage thermal effects by allowing slight air circulation around the wires. Using rigid or flexible conduits made of materials rated for embedded applications can reduce direct contact between warm wires and EPS, minimizing the risk of thermal degradation to the insulation foam.
Inspecting and Testing Wiring Installed Through EPS Panels
Visual Inspection of Installed Wiring
Before any electrical testing, a thorough visual inspection of the wiring routed through EPS panels is essential. This includes checking for proper placement within the channels cut into the EPS, ensuring wires are not pinched or kinked, and verifying that no sharp edges or debris could damage the insulation. Confirm that all protective conduits or sleeves, if used, are intact and correctly positioned to prevent direct contact with the EPS material.
Continuity and Insulation Resistance Testing
After visual verification, it is critical to perform continuity tests to ensure electrical paths are complete and uninterrupted. Using a multimeter, check that the conductors have no open circuits.
Equally important is the insulation resistance test, typically conducted with a megger or insulation resistance tester, to confirm that the wire insulation remains intact and has not been compromised during installation through the EPS panels. This prevents potential short circuits or electrical leakage that could pose safety hazards.
Test Type | Purpose | Tools Needed | Acceptable Criteria |
---|---|---|---|
Visual Inspection | Identify physical damage, proper placement, ensuring no deformation or damage to cables | Visual examination, flashlight | No visible damage, wires correctly seated and protected |
Continuity Test | Verify conductors are continuous and correctly connected | Multimeter or continuity tester | Complete circuit indicated by low resistance reading |
Insulation Resistance Test | Ensure insulation integrity and absence of leakage currents | Megger or insulation resistance tester | Resistance > 1 megaohm (commonly accepted threshold) |
Testing for Proper Grounding and Polarity
Verify ground continuity by checking the resistance between the ground conductor and the grounding electrode system. This ensures that in the event of a fault, electrical current will be safely diverted.
Additionally, confirm the correct polarity of the wiring using a polarity tester or a suitable multimeter setup to prevent hazardous reverse connections.
Thermal Monitoring During Initial Energizing
When first powering the wiring installed through EPS panels, performing a thermal scan with an infrared camera can identify hot spots indicative of loose connections or degraded insulation. Early detection of abnormal temperature variations helps to address issues before they result in damage to the wiring or EPS panels.
Documentation and Final Verification
Maintain thorough records of all inspection findings and test results for future reference and compliance with electrical codes. Final verification should ensure that all test values meet or exceed the recommended standards for safe operation within EPS panel installations.
Common Mistakes to Avoid When Running Wires Through EPS Panels
Improper Planning of Wiring Routes
One of the most frequent errors is inadequate planning of the wiring route within EPS panels. Failing to map out wire paths before installation can lead to unnecessary cutting, structural compromise, or difficulty in future maintenance. Always ensure that wiring paths are clearly defined, avoiding load-bearing areas and allowing ample space for insulation.
Cutting Channels Without Proper Tools or Techniques
Using inappropriate tools or aggressive techniques to cut channels in EPS panels can cause damage beyond the intended area, weakening the panel’s integrity. Avoid using sharp blades without guidance or excessive force. Instead, employ specialized hot-wire cutters or rotary tools with depth control to create clean, precise channels.
Neglecting Wire Protection Measures
Running wires directly against the EPS surface without protective conduit or sheathing is a common mistake. EPS panels are soft and can easily compress or abrade wires over time. Always use appropriate conduit or corrugated tubing to protect wiring from mechanical damage and to facilitate easier replacement if needed.
Overlooking Thermal Expansion and Moisture Considerations
Failing to account for the thermal expansion properties of EPS panels and potential moisture intrusion can compromise both electrical safety and panel performance. Wires should have enough slack to accommodate panel movement, and sealants or vapor barriers should be employed to prevent moisture ingress around wiring penetrations.
Insufficient Securing of Wires Inside Panels
Lack of proper securing methods can allow wires to shift inside the channels, leading to wear or disconnection. Use clips, staples, or cable ties rated for EPS applications to hold wiring firmly in place without compressing the insulation.
Not Testing Wiring After Installation
Installing wiring without rigorous inspection and testing can result in unnoticed faults or shorts. Always perform continuity and insulation resistance tests after running wires through EPS panels, ensuring electrical integrity and compliance with local codes.
Summary of Common Mistakes
Common Mistake | Potential Consequence | Recommended Avoidance Strategy |
---|---|---|
Poor planning of wiring routes | Structural damage, difficult maintenance | Careful route mapping before installation |
Incorrect cutting techniques | Panel integrity loss | Use specialized cutting tools and controlled methods |
No wire protection | Wire abrasion, electrical hazards | Install protective conduits or sheathing |
Ignoring thermal and moisture effects | Wire damage and insulation failure | Allow slack, seal penetrations properly |
Insufficient wire securing | Wires moving, wear and disconnections | Use appropriate fasteners designed for EPS |
Skipping post-installation testing | Undetected faults, safety risks | Conduct thorough electrical tests after wiring |